Pallet Racking: Optimizing Storage and Shelving in Industrial Goods and Services
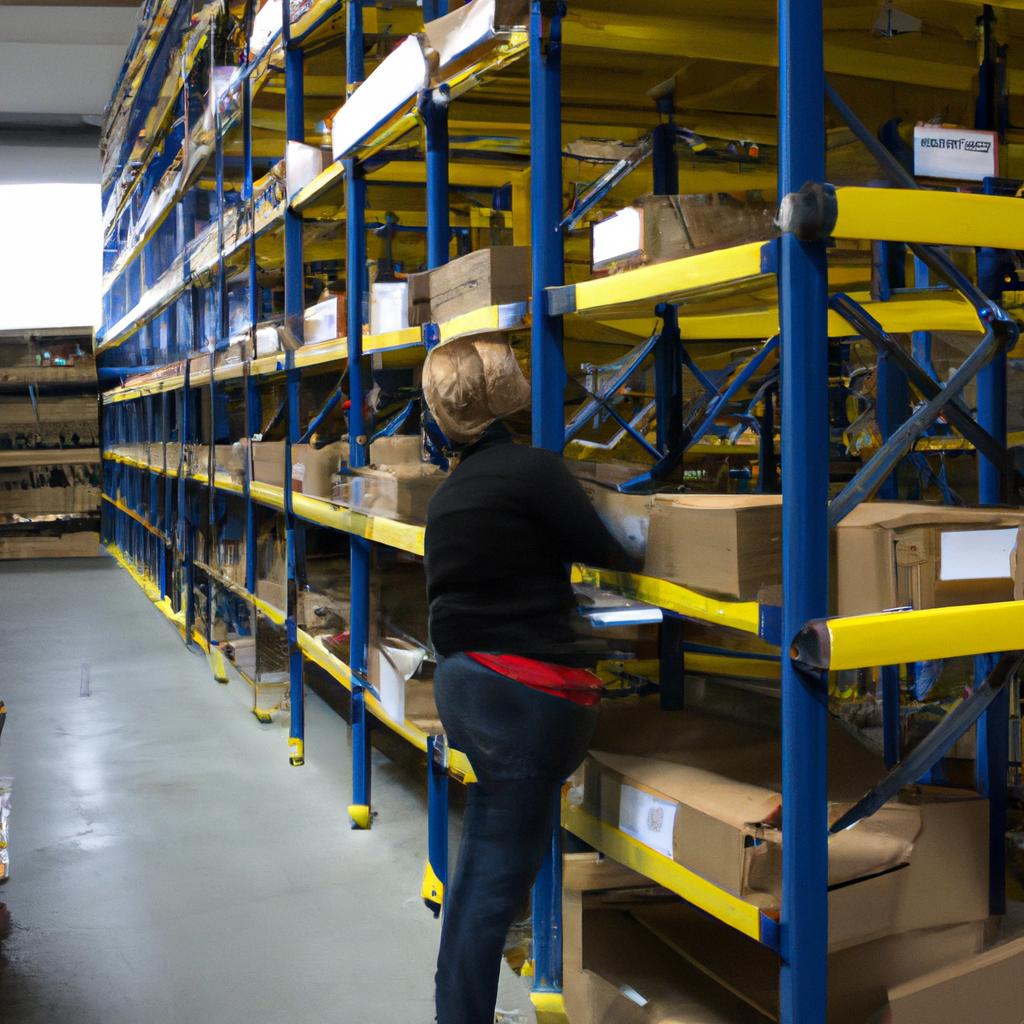
Pallet racking systems play a critical role in optimizing storage and shelving for industrial goods and services. These structures, designed to efficiently store palletized merchandise, have become an essential component of warehouses worldwide. For instance, consider the case of Company X, a leading manufacturer that experienced significant growth over the past few years. As their inventory expanded, they faced challenges with limited space and inefficient organization. By implementing a well-designed pallet racking system, Company X was able to maximize their available storage area while improving accessibility to their products.
Efficient storage management is crucial for businesses operating in the industrial sector as it directly impacts productivity and overall operational efficiency. Pallet racking offers an effective solution by providing a systematic approach to storing and retrieving goods within large-scale facilities. This article aims to explore the various benefits and considerations associated with pallet racking systems in order to assist organizations in making informed decisions about their storage infrastructure. Additionally, it will delve into different types of pallet racking configurations commonly used across industries, highlighting their advantages and potential drawbacks. Understanding these key elements will enable companies to optimize their storage capabilities, enhance workflow processes, and ultimately improve customer satisfaction through timely product delivery.
The Importance of Pallet Racking in Industrial Environments
When it comes to optimizing storage and shelving in industrial goods and services, pallet racking plays a crucial role. Imagine a bustling warehouse filled with various products waiting to be shipped out. Without an efficient storage system like pallet racking, chaos would ensue as items would be scattered haphazardly, making retrieval difficult and time-consuming.
To illustrate the importance of pallet racking, let’s consider a hypothetical scenario involving a logistics company that specializes in distributing consumer electronics. With hundreds of different products arriving daily, they needed a storage solution that could handle diverse shapes and sizes while maximizing space utilization. By implementing pallet racking systems tailored to their needs, this company was able to achieve remarkable efficiency gains. Products were organized systematically on sturdy racks, allowing for easy access during order fulfillment processes. This resulted in reduced labor costs and improved overall productivity.
There are several key reasons why businesses rely on pallet racking systems:
- Optimization of available space: Pallet racking enables vertical storage solutions, utilizing the full height of warehouses efficiently. This allows companies to make the most of their available square footage and prevent wastage caused by clutter or disorganized inventory.
- Enhanced accessibility: The use of pallets combined with well-designed rack structures provides straightforward access to stored items. Employees can quickly locate specific products without having to sift through piles or navigate tight spaces.
- Increased safety measures: Sturdy construction materials used in manufacturing modern pallet racks ensure stability even when carrying heavy loads. Implementing proper safety protocols such as securing loads correctly further reduces the risk of accidents related to falling objects.
- Scalability options: As businesses grow over time, so does their need for additional storage capacity. Pallet racking systems offer flexibility by allowing adjustments to accommodate changing requirements easily.
Pallet racking is undeniably vital in industrial environments due to its ability to optimize storage space, enhance accessibility, improve safety, and provide scalability options. In the subsequent section, we will explore different types of pallet racking systems to further understand how businesses can choose the most suitable solution for their specific needs.
Different Types of Pallet Racking Systems
Having established the significance of pallet racking in industrial environments, it is now crucial to delve into the various types of systems available. By understanding these options, businesses can make informed decisions about which pallet racking system best suits their specific needs and maximizes their storage capabilities. To illustrate this further, let’s consider an example.
Case Study:
Company XYZ operates a large manufacturing facility that produces automotive parts for global distribution. With an ever-growing inventory, they needed a storage solution that would not only optimize space utilization but also provide easy access to products during order fulfillment processes. After thorough research and consultation with industry experts, they decided to implement a selective pallet racking system due to its versatility and efficiency.
Types of Pallet Racking Systems:
To help you understand the range of choices available when it comes to pallet racking systems, here are some common options:
- Selective Pallet Racking: Offers direct access to every individual pallet stored.
- Drive-In/Drive-Through Racking: Maximizes storage capacity by allowing forklifts to drive directly into the rack structure.
- Push Back Racking: Utilizes inclined rails and carts to allow for storing multiple pallets deep on each level.
- Cantilever Racking: Specifically designed for long or irregularly shaped items such as pipes or lumber.
Consider the following benefits that come with implementing an efficient pallet racking system:
- Increased productivity through streamlined operations.
- Improved warehouse safety by reducing cluttered spaces.
- Enhanced inventory control leading to more accurate stock management.
- Cost-effective solutions resulting from better space utilization.
Table Example (Markdown Format):
Pallet Racking System | Features | Ideal for |
---|---|---|
Selective | Direct access to every pallet | Fast-moving inventory |
Drive-In/Drive-Through | High storage density | Bulk goods |
Push Back | Multiple pallets per level | Time-sensitive perishable products |
Cantilever | Storage of long or irregularly shaped items | Building materials, furniture |
In conclusion, selecting the right type of pallet racking system is crucial for efficient and effective storage management. By carefully considering factors such as product types, inventory turnover rates, and available space, companies can optimize their warehouse operations and maximize productivity.
Transition into subsequent section:
Now let’s turn our attention to the important factors that need to be considered when selecting an ideal pallet racking system for your specific requirements.
Factors to Consider When Choosing Pallet Racking
Optimizing storage and shelving in industrial goods and services is crucial for maximizing efficiency and productivity. In the previous section, we explored different types of pallet racking systems commonly used in warehouses and industrial settings. Now, let’s delve into the factors that should be considered when choosing pallet racking.
To illustrate these considerations, let’s imagine a hypothetical scenario where a distribution center needs to optimize its storage space for various products, ranging from small electronic components to large automotive parts. The goal is to streamline operations by implementing an efficient pallet racking system.
One important factor to consider is the weight capacity of the racks. Different products have varying weights, so it is essential to choose pallet racking that can safely support heavy loads without compromising stability or safety. For example, if the distribution center regularly handles heavy machinery parts weighing several tons each, selecting robust rack systems with high weight capacities will be imperative.
Another consideration is accessibility. Efficient retrieval and placement of goods play a significant role in reducing operational downtime. Selecting a suitable pallet racking system that allows easy access to items can enhance workflow efficiency. For instance, using selective pallet racking would provide direct access to every individual pallet stored within the system, making it ideal for distributing smaller electronic components.
Additionally, warehouse layout optimization should not be overlooked when choosing pallet racking systems. Factors such as available floor space and ceiling height must be taken into account to maximize storage density while ensuring proper clearance for equipment like forklifts or reach trucks. By utilizing advanced planning software or consulting experts experienced in warehouse optimization, businesses can determine the most effective arrangement tailored to their specific needs.
Considerations When Choosing Pallet Racking:
- Weight Capacity: Ensure adequate support for heavy loads
- Accessibility: Optimize retrieval and placement efficiency
- Warehouse Layout: Maximize storage density while accommodating equipment clearance
By carefully considering these factors during the selection process, businesses can implement an optimized pallet racking system that enhances storage capacity, accessibility, and overall efficiency.
Maximizing Space and Efficiency with Pallet Racking
Optimizing Storage and Shelving in Industrial Goods and Services
Factors to Consider When Choosing Pallet Racking:
In the previous section, we discussed the various factors that one should consider when choosing pallet racking for their industrial goods and services. Now, let us delve further into how businesses can maximize space and efficiency with this storage solution.
Imagine a large warehouse filled with products waiting to be stored. Without an effective system in place, chaos would ensue, making it difficult to locate specific items or retrieve them efficiently. This is where pallet racking comes into play. By utilizing vertical space and organizing products on sturdy shelves, companies can optimize their storage capacity while streamlining operations.
To achieve maximum space utilization and enhance operational efficiency, businesses must take into account several key considerations:
-
Accessibility: It is crucial to arrange inventory in a way that facilitates easy access to all items. By implementing selective pallet racking systems, which allow direct access to each individual pallet, workers can quickly locate and retrieve products as needed.
-
Weight Capacity: The weight-bearing capabilities of your chosen pallet racking system are of utmost importance. Different types of racks have varying load capacities; therefore, it is essential to assess the weight requirements of your inventory before selecting a suitable option.
-
Flexibility: Businesses often experience changes in product demand or may need to accommodate different sizes or shapes of merchandise over time. Opting for adjustable pallet racking allows for flexibility in accommodating these variations without requiring significant modifications or investments.
-
Safety Measures: Ensuring safety within the warehouse environment should always be a top priority. Features such as rack guards, column protectors, and safety netting help prevent accidents caused by falling objects or collisions between equipment and shelving units.
By considering these factors carefully during the selection process, businesses can significantly improve their storage capabilities while maintaining efficient operations.
Maximizing Space Efficiency with Pallet Racking:
To further illustrate the benefits of pallet racking in optimizing storage and shelving, let us examine a hypothetical case study:
Suppose Company XYZ operates a large distribution center that deals with various products. They implement selective pallet racking systems throughout their warehouse to maximize space usage effectively. By doing so, they experience the following advantages:
- Increased Storage Capacity: With vertical stacking capabilities, Company XYZ can store more items within the same square footage.
- Enhanced Organization: The adoption of pallet racking ensures systematic categorization and easy identification of products, leading to improved inventory management and reduced search time.
- Efficient Space Utilization: By utilizing the height of their facility through taller racks, Company XYZ minimizes wasted vertical space and optimizes their storage capacity.
- Streamlined Operations: Quick access to individual pallets facilitates faster order picking and fulfillment processes.
In conclusion, choosing the right type of pallet racking system is essential for businesses aiming to optimize their storage and shelving operations. Considering factors such as accessibility, weight capacity, flexibility, and safety measures will enable companies to make informed decisions regarding their warehouse setup.
Safety Considerations for Pallet Racking:
Now that we have explored how selecting appropriate pallet racking solutions can enhance efficiency in industrial goods and services settings let us shift our focus towards ensuring safe working environments surrounding these installations.
Safety Considerations for Pallet Racking
Building upon the principles of maximizing space and efficiency with pallet racking, it is crucial to address the safety considerations involved in implementing such systems. By prioritizing safety measures, businesses can ensure a secure working environment while optimizing their storage capabilities.
To illustrate the importance of safety in pallet racking, let us consider the hypothetical case study of a logistics warehouse that neglected proper safety protocols. Due to insufficient training and inadequate maintenance procedures, an accident occurred where a poorly stacked pallet collapsed, causing damage to goods and endangering workers. This unfortunate event highlights the need for comprehensive safety guidelines when utilizing pallet racking systems.
There are several key factors to consider when ensuring the safe operation of pallet racking installations:
- Load Capacity: Always adhere to load capacity limits specified by manufacturers. Overloading racks not only compromises structural integrity but also increases the risk of accidents.
- Regular Inspections: Conduct routine inspections to identify any signs of wear and tear or damage caused by impacts. Prompt repairs or replacements should be undertaken immediately.
- Proper Training: Provide thorough training sessions for employees on correct loading techniques, equipment usage, and emergency evacuation procedures.
- Clear Signage: Clearly label rack capacities and aisle restrictions using standardized signage throughout your facility. This ensures that personnel understand weight limitations and promotes a safer work environment.
Table – Common Safety Guidelines for Pallet Racking Systems:
Safety Guideline | Importance |
---|---|
Perform regular inspections | High |
Train employees adequately | Medium |
Adhere to manufacturer’s load limits | High |
Implement clear signage | Medium |
By incorporating these safety considerations into day-to-day operations, companies can mitigate risks associated with pallet racking systems while maintaining optimal storage solutions.
With a focus on safety established, our next section will delve into the essential aspects of maintenance and upkeep of pallet racking systems, ensuring their longevity and continued efficiency.
Maintenance and Upkeep of Pallet Racking Systems
Having discussed the safety considerations for pallet racking, it is now essential to delve into the crucial aspect of maintenance and upkeep. Proper maintenance ensures the longevity and optimal performance of pallet racking systems in industrial goods and services settings. To illustrate this point, let’s consider a hypothetical case study involving a manufacturing facility that neglected regular maintenance practices.
In this hypothetical scenario, the manufacturing facility failed to conduct routine inspections and repairs on their pallet racking system over an extended period. As a result, they experienced several issues such as damaged beams, misaligned frames, and weakened support structures. These problems not only compromised the overall stability of the storage system but also increased the risk of accidents or product damage.
To avoid such detrimental consequences, specific precautions must be taken to maintain pallet racking systems effectively:
- Regular Inspections: Conducting periodic inspections helps identify any signs of wear and tear, including bent or cracked components.
- Repairs and Replacements: Promptly address any identified issues by repairing or replacing damaged parts to ensure structural integrity.
- Load Capacity Monitoring: Continuously monitor load capacities to prevent overloading which can lead to excessive stress on the racking system.
- Training and Education: Provide comprehensive training programs for employees involved in handling materials stored on pallet racks to promote proper usage techniques.
Furthermore, implementing a well-defined maintenance schedule is critical for ensuring consistent upkeep. The table below outlines some key tasks that should be included in such a schedule:
Task | Frequency | Responsible Party |
---|---|---|
Visual inspection | Monthly | Warehouse staff |
Structural analysis | Biannually | Qualified engineer |
Component replacement | As needed | Maintenance team |
Load capacity review | Quarterly | Operations manager |
By adhering to these recommended practices and scheduling regular maintenance activities, businesses can minimize the risk of accidents, enhance operational efficiency, and extend the lifespan of their pallet racking systems.
In summary, maintaining and regularly inspecting pallet racking systems is crucial for ensuring safety and optimal performance in industrial goods and services environments. Through diligent upkeep practices, businesses can mitigate potential risks and prevent costly structural failures. By investing time and resources into maintenance activities, companies demonstrate their commitment to workplace safety while also safeguarding their valuable inventory and storage infrastructure.