Packaging Machinery in Industrial Goods and Services: A Comprehensive Overview
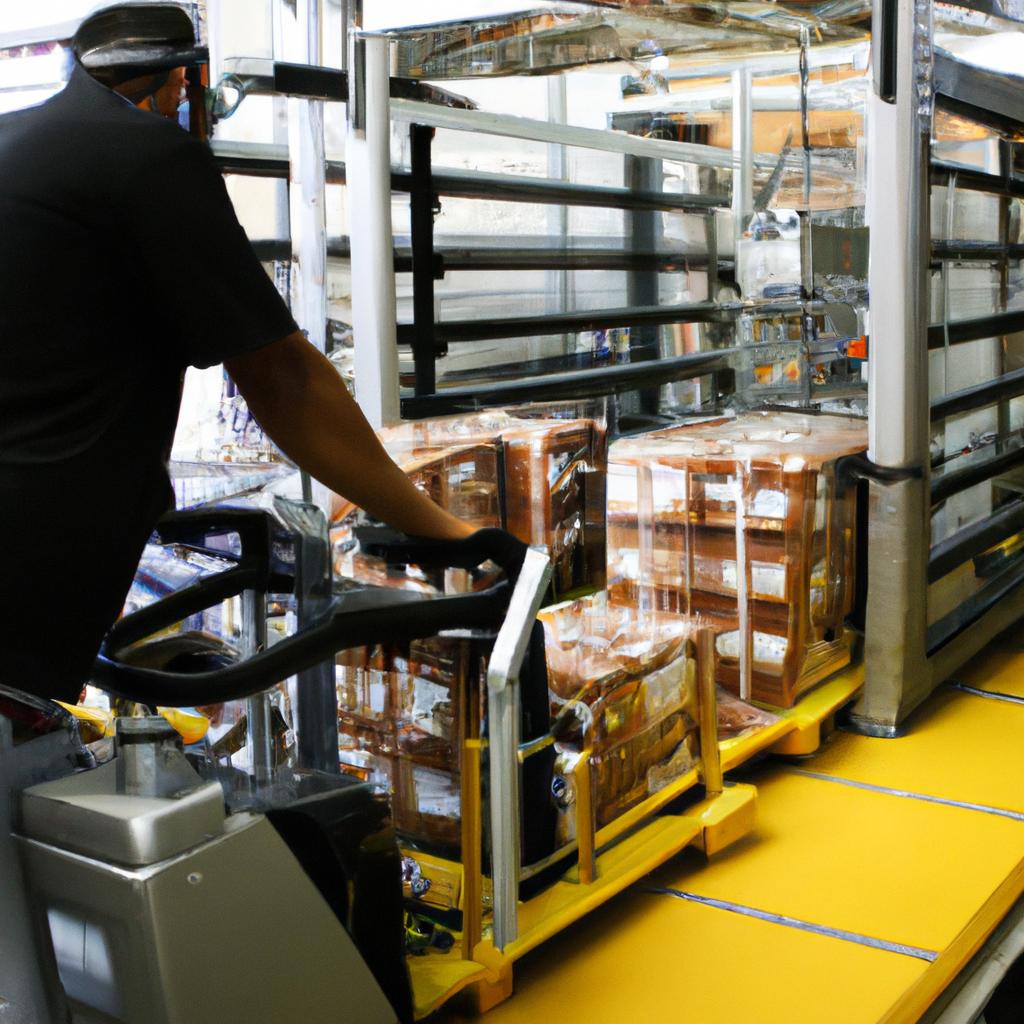
The efficient and effective packaging of goods is a crucial aspect of modern industrial operations. Packaging machinery plays a pivotal role in the manufacturing sector, facilitating the process of sorting, filling, sealing, labeling, and wrapping products for distribution. For instance, imagine a hypothetical scenario where Company X produces thousands of food packages daily to meet consumer demands. Without advanced packaging machinery, this task would be arduous and time-consuming, leading to delays in product delivery and potential customer dissatisfaction.
In light of these considerations, it becomes evident that understanding packaging machinery is essential for businesses operating in the realm of industrial goods and services. In this comprehensive overview article, we will delve into various aspects related to packaging machinery’s significance in the industrial sector. Firstly, we will explore the different types of packaging machines commonly utilized across industries, ranging from fillers and sealers to labelers and wrappers. Secondly, we will examine their operational mechanisms and highlight key features that contribute to their efficiency. Lastly, we will discuss emerging trends in packaging machinery technology and its implications for businesses seeking to enhance productivity while meeting evolving market demands.
By examining the multifaceted nature of packaging machinery within the context of industrial goods and services, this article aims to provide readers with valuable insights into how these machines can streamline the packaging process and contribute to overall operational efficiency.
Packaging machinery encompasses a wide range of equipment designed to automate various tasks involved in the packaging process. One essential type of packaging machine is the filler, which dispenses precise amounts of product into containers, ensuring accurate measurements and reducing waste. This is especially crucial in industries such as food and pharmaceuticals where precision is vital.
Sealers are another critical category of packaging machines that create airtight seals on packages, preventing spoilage or contamination. These machines utilize different sealing methods depending on the packaging material, including heat sealing, ultrasonic sealing, and induction sealing.
Labelers play a key role in providing product information and branding by applying labels to packages accurately. They can handle different label sizes and shapes, ensuring consistency and professionalism in labeling.
Wrapping machines are used to securely wrap products with stretch film or shrink film for protection during transportation. These machines efficiently bundle products together while minimizing material usage.
The operational mechanisms of packaging machines vary depending on their specific functions. Some machines operate using mechanical components such as conveyors, gears, and pistons, while others incorporate advanced technologies like robotics and automation systems for enhanced productivity.
Efficiency-enhancing features are integral to modern packaging machinery. For example, many machines now have programmable logic controllers (PLCs) that enable operators to program precise settings for each packaging task. This reduces human error and ensures consistency in production.
Moreover, advancements in sensor technology have enabled machines to detect issues such as package misalignment or missing components automatically. These smart sensors can trigger corrective actions or halt operations until the problem is resolved.
In terms of emerging trends, the adoption of robotics has revolutionized the packaging industry. Robotic arms equipped with vision systems can handle complex tasks like picking varying-sized objects from a conveyor belt quickly and accurately. Collaborative robots (cobots) work alongside human workers safely, increasing efficiency without sacrificing safety.
Furthermore, there’s a growing emphasis on sustainability in packaging machinery. Manufacturers are integrating eco-friendly features, such as reduced material usage and recyclable packaging options, to align with consumer demands for environmentally conscious practices.
In conclusion, packaging machinery is crucial in the industrial sector as it streamlines the packaging process, ensures accuracy and consistency, and enhances overall operational efficiency. Understanding the different types of machines available, their operational mechanisms, and emerging trends enables businesses to make informed decisions when investing in packaging machinery to meet market demands effectively.
Types of Packaging Machinery
Packaging machinery plays a crucial role in various industries by automating the packaging process and ensuring efficiency. There are several types of packaging machinery used, each designed to handle specific tasks and meet different requirements. To illustrate this concept, let’s consider an example of a beverage manufacturing company that produces bottled drinks.
One type of packaging machinery commonly used in such companies is the filling machine. This machine automatically fills bottles with the desired amount of liquid, eliminating the need for manual labor and reducing human error. The filling machine ensures precise measurement and consistent quality control, resulting in uniform product presentation. In our hypothetical case study, this machinery would allow the beverage manufacturer to fill hundreds or even thousands of bottles per hour accurately.
To provide further insight into the diversity of packaging machinery available, here is a bullet point list highlighting some common types:
- Capping machines: These machines securely seal containers by applying caps or lids.
- Labeling machines: They apply labels onto products, providing essential information such as branding and ingredients.
- Wrapping machines: These equipment wrap products in protective materials like shrink films or stretch wraps.
- Palletizing machines: They automate the stacking and arrangement of packaged goods on pallets for safe transportation.
Now let us delve deeper into these types with a table demonstrating their functionalities:
Type | Functionality |
---|---|
Filling Machine | Accurately measures and dispenses liquids into containers |
Capping Machine | Applies caps or lids tightly onto containers |
Labeling Machine | Attaches labels onto products for identification |
Wrapping Machine | Encloses products in protective materials |
Palletizing Machine | Stacks packaged goods on pallets for efficient transport |
In summary, packaging machinery encompasses various types specifically designed to streamline production processes across multiple industries. With examples like filling machines catering to bottling needs within beverage manufacturing, it is evident that these machines greatly enhance productivity and accuracy. In the subsequent section, we will explore the key components of packaging machinery, shedding light on their essential functionalities and contributions to industrial goods and services.
Key Components of Packaging Machinery
Transitioning from the previous section on the different types of packaging machinery, let us now delve into the key components that make up these sophisticated machines. To illustrate their importance, consider a hypothetical scenario where Company XYZ is a leading manufacturer of packaged food products. In order to meet increasing consumer demand and maintain product quality standards, Company XYZ invests in state-of-the-art packaging machinery.
The performance of packaging machinery relies on several crucial components that work together seamlessly. First and foremost, the control system plays a pivotal role in regulating various machine functions. This includes monitoring production speed, adjusting settings for different packaging materials, and ensuring overall operational efficiency. The control system acts as the brain behind the machinery, enabling smooth coordination between mechanical parts and electronic sensors.
Secondly, motors are integral to driving the movement of different machine mechanisms such as conveyor belts and sealing rollers. These motors provide precise torque and speed control to ensure accurate positioning of packages during filling or sealing processes. By maintaining consistent motion, they contribute significantly to reducing errors and enhancing productivity.
Thirdly, sensors play a vital role in detecting irregularities throughout the packaging process. For instance, optical sensors can identify empty containers or verify correct labeling placement before sealing. Pressure sensors can monitor proper air pressure levels within pneumatic systems to prevent leaks or malfunctions. Such advanced sensing technologies not only enhance product safety but also minimize wastage by promptly identifying any issues.
Lastly, specialized tooling sets enable customization based on specific product requirements while ensuring reliable performance. Tooling sets consist of molds or dies designed for shaping packages according to desired dimensions and designs. With adjustable features like interchangeable parts or adjustable cutting blades, tooling sets accommodate diverse packaging needs efficiently and accurately.
To appreciate further how these key components contribute holistically to efficient packaging operations using modern machinery, let us explore some emotional responses:
- Reliability: Imagine relying on outdated equipment prone to frequent breakdowns versus utilizing top-notch machinery with robust control systems and dependable motors.
- Precision: Consider the satisfaction of ensuring precise measurements and accurate labeling through sophisticated sensing technologies, enhancing the overall product presentation.
- Efficiency: Picture a scenario where packaging processes are optimized, reducing production time and costs while meeting increasing consumer demands seamlessly.
- Safety: Reflect on the peace of mind resulting from employing machinery with advanced tooling sets that ensure secure packaging for products.
To summarize, by understanding the essential components that make up packaging machinery, it becomes evident how these machines contribute to efficient operations. The control system acts as the foundation of coordination, while motors provide motion precision. Sensors detect irregularities swiftly, and specialized tooling sets allow customization based on specific requirements. With this knowledge in mind, we can now explore further the benefits of utilizing such technology in the subsequent section focused on “Benefits of Using Packaging Machinery.”
Benefits of Using Packaging Machinery
In the previous section, we explored the key components that make up packaging machinery. Now, let’s delve deeper into the benefits of utilizing this sophisticated equipment in various industries.
Imagine a scenario where a food processing company is experiencing challenges in meeting their production targets due to manual packing processes. By incorporating packaging machinery into their operations, they can significantly enhance efficiency and productivity. This real-world example showcases how adopting automated packaging solutions can revolutionize manufacturing processes across industries.
The advantages of using packaging machinery are numerous and impactful:
- Increased Speed and Productivity: Automated packaging machines can handle high volumes of products at an accelerated pace, resulting in faster production cycles and increased output.
- Enhanced Accuracy and Consistency: These machines ensure precise measurements, consistent product placement, and reliable seal integrity, minimizing errors while maintaining quality control standards.
- Improved Safety Measures: Packaging machinery incorporates advanced safety features such as sensors and emergency stop buttons to mitigate potential hazards for both operators and products.
- Cost Savings: While initial investment costs may be higher than manual labor, automation ultimately reduces long-term expenses by decreasing reliance on human resources, lowering material waste, and optimizing overall operational efficiency.
To further illustrate these benefits visually:
Benefit | Description |
---|---|
Increased Speed | Packaging machinery enables rapid processing speeds compared to manual methods. |
Enhanced Accuracy | The precision of automated systems ensures accurate product measurement and placement. |
Improved Safety | Advanced safety features protect both workers operating the machinery and the packaged goods themselves. |
Cost Savings | Automation leads to reduced labor costs over time while increasing overall operational efficiency. |
These benefits demonstrate why many companies choose to invest in packaging machinery for their industrial needs. In our next section, we will explore factors that should be considered when selecting the right type of packaging machinery for specific applications.
Transitioning smoothly into the subsequent section about “Factors to Consider When Choosing Packaging Machinery,” it is crucial to carefully evaluate several essential aspects. By doing so, businesses can make informed decisions and maximize the benefits of implementing packaging machinery in their operations.
Factors to Consider When Choosing Packaging Machinery
Imagine a scenario where a manufacturing company is looking to upgrade its packaging process by investing in new machinery. The decision-making process involves careful consideration of various factors, as the right choice can significantly impact productivity and overall efficiency. In this section, we will explore some key considerations that should be taken into account when selecting packaging machinery.
Factors to Consider:
-
Production Volume and Speed:
The first factor to consider is the production volume and speed requirements of your specific operation. It is crucial to determine the expected output per hour or day and select machinery that can handle these demands effectively. For example, if your company produces large quantities of goods within tight deadlines, opting for high-speed packaging equipment would be essential to meet customer expectations and maintain competitiveness. -
Product Characteristics:
Different products have varying characteristics that may influence the selection of appropriate packaging machinery. Factors such as size, shape, weight, fragility, and perishability need to be carefully assessed. For instance, delicate items might require specialized handling mechanisms or protective measures during the packaging process. By considering these product-specific requirements, you can ensure that the chosen machinery aligns with both operational needs and end-product quality standards. -
Flexibility and Adaptability:
In today’s dynamic business landscape, adaptability plays a vital role in sustaining growth and responding to changing consumer demands swiftly. When choosing packaging machinery, it is important to assess its flexibility in accommodating different product sizes, shapes, or materials efficiently without compromising performance or requiring excessive adjustments between batches. A versatile machine enables smooth transitions between diverse product lines while minimizing downtime associated with reconfiguration. -
Cost Analysis:
Investing in packaging machinery involves evaluating both initial costs and long-term benefits. While it may be tempting to focus solely on upfront expenses, taking into account ongoing maintenance costs, energy consumption rates, spare part availability/costs, training requirements for operators/technicians, and expected lifespan is crucial. Conducting a comprehensive cost analysis helps in determining the total ownership costs over a machine’s lifespan and making an informed decision that aligns with budgetary constraints.
- Increased operational efficiency
- Enhanced product quality assurance
- Reduced labor requirements
- Improved customer satisfaction
Emotional Impact Table:
Factors Considered | Emotional Impact |
---|---|
Production Volume | Efficiency |
Product Characteristics | Quality Assurance |
Flexibility & Adaptability | Versatility |
Cost Analysis | Financial Stability |
Concluding Paragraph:
By carefully considering production volume and speed, product characteristics, flexibility and adaptability, as well as conducting a thorough cost analysis, manufacturers can make informed decisions while selecting packaging machinery. These considerations contribute to maximizing productivity, ensuring product integrity, remaining agile in response to market demands, and optimizing resource allocation. In the following section on “Packaging Machinery Maintenance and Troubleshooting,” we will delve into the importance of proactive maintenance practices to ensure uninterrupted operations and address common issues that may arise during equipment usage.
Packaging Machinery Maintenance and Troubleshooting
Imagine a scenario where a manufacturing company relies heavily on packaging machinery to efficiently package its products. One day, the machine suddenly malfunctions, causing a halt in production and potentially leading to financial losses. This example highlights the importance of understanding packaging machinery maintenance and troubleshooting techniques. In this section, we will explore key considerations for maintaining packaging machinery effectively.
To ensure smooth operation and maximize productivity, regular maintenance is crucial. Here are some factors to consider when performing maintenance on packaging machinery:
- Preventive Maintenance: Implementing routine checks and inspections can help identify potential issues before they escalate into major problems. Regularly lubricating moving parts, inspecting belts and chains for wear and tear, and cleaning sensors can prevent breakdowns.
- Training Programs: Providing comprehensive training programs for operators can enhance their knowledge of the equipment’s functionality and enable them to detect early signs of malfunction. Offering refresher courses periodically ensures that employees stay up-to-date with best practices.
- Documentation: Developing detailed documentation outlining maintenance procedures, schedules, spare part inventories, and troubleshooting guides allows technicians to perform tasks effectively. Keeping accurate records also helps track any recurring issues or patterns.
- Collaborative Approach: Encouraging open communication between operators and maintenance personnel fosters teamwork in addressing challenges promptly. Operators should be encouraged to report any irregularities immediately so that appropriate action can be taken.
In addition to regular maintenance, it is essential to have effective troubleshooting strategies in place when unexpected issues arise during production. The following table provides an overview of common packaging machinery problems alongside possible solutions:
Problem | Possible Solution |
---|---|
Machine Jamming | Clear blockages by removing debris or adjusting settings |
Misaligned Components | Realign parts according to manufacturer guidelines |
Sensor Malfunction | Clean or replace faulty sensors |
Electrical Failures | Check power supply connections; inspect fuses and wiring |
By adhering to these maintenance practices and having troubleshooting strategies readily available, manufacturers can minimize downtime caused by packaging machinery issues. Keeping production running smoothly not only prevents financial losses but also ensures customer satisfaction through timely delivery of products.
Looking ahead, the field of packaging machinery is continuously evolving.
Future Trends in Packaging Machinery
In the previous section, we discussed the importance of packaging machinery maintenance and troubleshooting. Now, let us delve deeper into some key aspects that are essential for ensuring smooth operations in this field.
To illustrate the significance of effective maintenance practices, consider a hypothetical scenario where a manufacturing company experiences frequent breakdowns with their packaging machine due to improper maintenance. This leads to delays in production schedules, increased downtime, and ultimately results in customer dissatisfaction. However, by implementing regular preventive maintenance measures such as lubrication checks and component inspections, these issues can be minimized or even eliminated entirely.
When it comes to troubleshooting packaging machinery, having a systematic approach is crucial. To assist technicians in identifying and resolving problems efficiently, here are four critical steps:
- Gather information: Begin by collecting as much relevant data about the issue as possible – including error codes received, specific symptoms observed during malfunctioning, and any recent changes made to the system.
- Perform diagnostics: Utilize diagnostic tools or software provided by manufacturers to identify potential causes of the problem accurately.
- Isolate the issue: Once potential causes have been identified, isolate each one through testing or inspection until the root cause is determined.
- Resolve and test: After isolating the problem area, take appropriate actions to resolve it based on manufacturer guidelines or expert advice. Finally, thoroughly test the machine after repairs to ensure proper functionality.
For a comprehensive understanding of common troubleshooting scenarios encountered in packaging machinery operations, refer to Table 1 below:
Problem | Possible Cause | Solution |
---|---|---|
Misalignment | Worn-out belts | Replace belts |
Irregular sealing | Temperature fluctuations | Adjust temperature settings |
Jammed conveyor | Overloaded load capacity | Reduce load weight |
Inconsistent labeling | Faulty sensors | Replace or recalibrate sensors |
Table 1: Common troubleshooting scenarios and their solutions in packaging machinery operations.
By following a methodical approach to maintenance and troubleshooting, companies can significantly reduce downtime, enhance productivity, and improve customer satisfaction. Implementing regular preventive measures and utilizing effective diagnostic techniques are vital for maintaining optimal performance of packaging machinery.
In conclusion, the successful operation of packaging machinery relies heavily on routine maintenance practices and efficient troubleshooting methods. Through diligent monitoring, prompt intervention, and adherence to manufacturer guidelines, businesses can ensure smooth functioning of these machines while minimizing costly disruptions in production processes.