Metalworking Machinery: Enhancing Industrial Processes
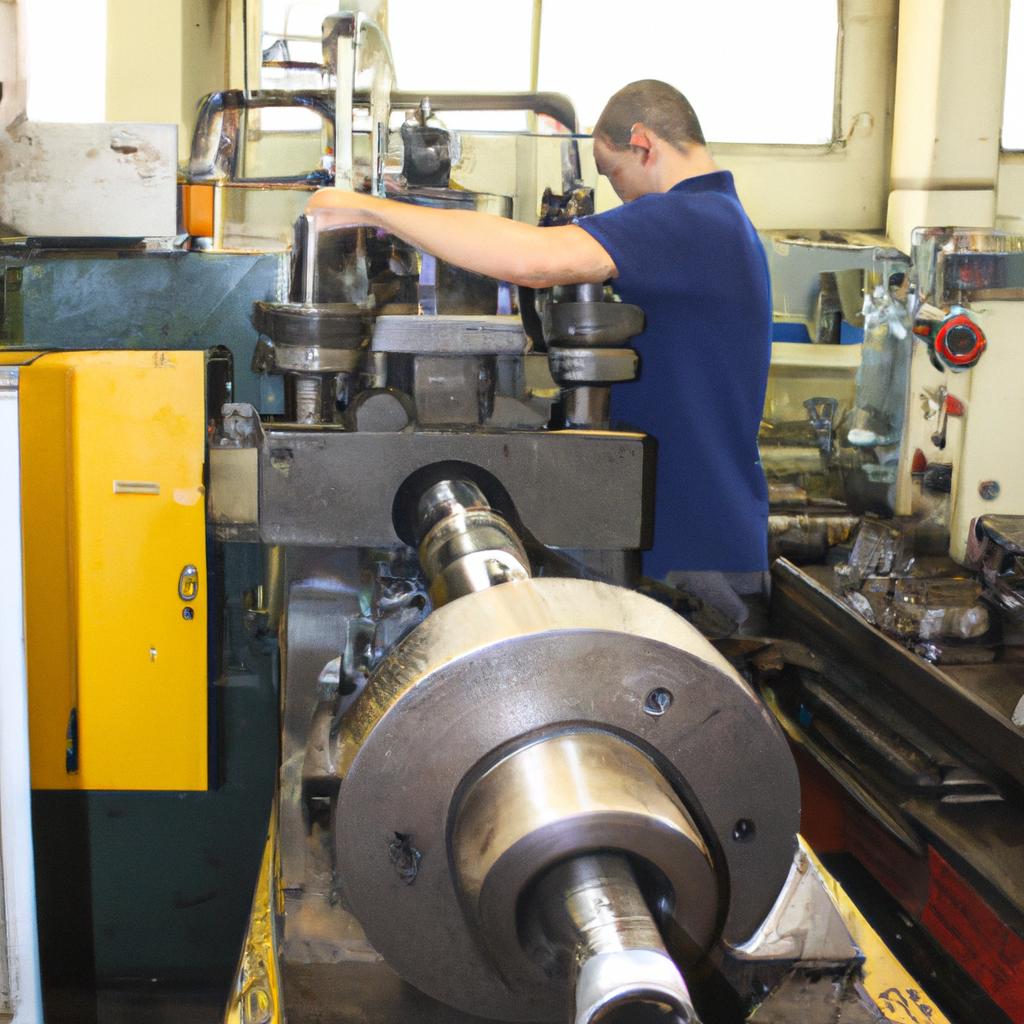
The use of metalworking machinery has become increasingly prominent in various industrial processes, revolutionizing the way manufacturing and production are conducted. These machines have proven to be invaluable tools for enhancing efficiency, precision, and productivity within the industrial sector. For instance, consider a hypothetical scenario where a manufacturer is tasked with producing intricate components for aerospace applications. By employing advanced metalworking machinery such as CNC milling machines and laser cutting systems, they can achieve highly accurate results while minimizing human error.
In recent years, the advancements in metalworking machinery technology have significantly impacted industries ranging from automotive manufacturing to construction. The introduction of computer-controlled systems has facilitated automation and process optimization, allowing for faster production cycles without compromising on quality or safety standards. Moreover, these machines enable manufacturers to work with an extensive range of materials including aluminum alloys, stainless steel, copper, and titanium – each requiring specific machining techniques depending on their properties. As a result, companies can explore new possibilities in terms of design complexity and material utilization.
Metalworking machinery plays a crucial role in shaping modern industries by offering enhanced capabilities that were previously unattainable through traditional manual methods. This article aims to delve into the different types of metalworking machinery available today and analyze how they contribute to improving industrial processes across diverse sectors.
Understanding the Importance of Metalworking Machinery
Metalworking machinery plays a vital role in enhancing industrial processes across various sectors. Consider, for example, a manufacturing company that specializes in producing automotive components. Without access to efficient metalworking machinery, such as CNC machines and laser cutters, this company would struggle to meet production demands and maintain the required level of precision.
The significance of metalworking machinery can be better understood by considering its numerous advantages. Firstly, these machines enable manufacturers to automate various tasks, improving productivity and reducing labor costs. With automated processes, companies can achieve higher levels of accuracy and consistency in their products, resulting in improved quality control. Secondly, metalworking machinery enables faster turnaround times by reducing manual processing time significantly. This increased efficiency allows businesses to deliver products promptly and stay competitive in the market.
To further emphasize the importance of metalworking machinery, consider the following bullet points:
- Increased productivity: Metalworking machinery streamlines operations and reduces human error.
- Enhanced precision: These machines provide high levels of accuracy during cutting, shaping, and forming processes.
- Cost savings: By automating tasks and minimizing waste materials, metalworking machinery helps reduce expenses.
- Improved safety: Advanced features like automatic shut-off mechanisms enhance workplace safety for operators.
Additionally, a table showcasing different types of metalworking machinery along with their functions can illustrate the diverse range of capabilities available:
Type | Function |
---|---|
CNC Machines | Computer-controlled machining for precise cuts |
Laser Cutters | High-powered lasers used for accurate cutting |
Press Brakes | Bending or folding sheet metal |
Welding Equipment | Joining metals together through fusion |
In conclusion (transition), understanding the importance of metalworking machinery is essential for appreciating how it revolutionizes industrial processes across multiple sectors. In the subsequent section about “Types of Metalworking Machinery and Their Functions,” we will delve deeper into the specific machines and their respective functions, exploring how they contribute to enhancing productivity and driving innovation in various industries.
Types of Metalworking Machinery and Their Functions
Metalworking machinery plays a crucial role in enhancing industrial processes across various sectors. By efficiently shaping, cutting, and forming metal materials, these machines contribute to the production of high-quality products that meet industry standards. To illustrate the significance of metalworking machinery, let us consider an example scenario: a manufacturing company specializing in automotive parts.
In this hypothetical case study, the manufacturing company relies on metalworking machinery to produce components for automobile engines. The precision and accuracy provided by machines such as CNC (Computer Numerical Control) mills and lathes are essential in creating intricate designs with tight tolerances required for optimal engine performance. Without access to advanced metalworking machinery, the company would struggle to meet demand while maintaining consistency in product quality.
To further understand the importance of metalworking machinery, it is helpful to explore its different functions. Here are some key aspects:
-
Shaping and Forming: Metalworking machinery allows for precise shaping and forming of raw materials into desired shapes or structures. Processes like bending, rolling, and forging enable manufacturers to create complex geometries required for specific applications.
-
Cutting and Machining: Machines like bandsaws, milling machines, and laser cutters facilitate accurate cutting of metals into desired sizes or shapes. These tools help reduce material waste and increase overall efficiency during production.
-
Joining Techniques: Welding equipment enables the fusion of separate metal pieces into a single entity, ensuring strong connections between components. This technique is vital in industries where structural integrity is crucial, such as construction or aerospace.
-
Surface Finishing: Machinery used for grinding, polishing, or coating enhances the final appearance and functionality of metal products by providing smooth finishes or protective layers against corrosion.
The following table showcases the emotional impact created through incorporating visual elements:
| Emotion | Reason | Example |
| ------------- | ---------------------------------- | ---------------------------------- |
| Satisfaction | Improved productivity | Meeting deadlines effortlessly |
| Efficiency | Reduced manual labor | Increased production output |
| Confidence | Consistent product quality | Meeting industry standards |
| Innovation | Technological advancements | Incorporating automation features |
In conclusion, metalworking machinery is indispensable for industries seeking to enhance their manufacturing processes. Through various functions like shaping, cutting, joining, and surface finishing, these machines enable precise and efficient fabrication of metal components. In the subsequent section about “Advancements in Metalworking Machinery Technology,” we will explore how technological innovations have further revolutionized this field.
Advancements in Metalworking Machinery Technology
Section H2: Advancements in Metalworking Machinery Technology
In recent years, advancements in metalworking machinery technology have revolutionized industrial processes, enhancing efficiency and productivity. These innovations have allowed manufacturers to achieve unprecedented levels of precision and quality in their operations. To exemplify the impact of these advancements, let us consider a hypothetical case study involving a manufacturing company specializing in automotive components.
One significant advancement is the integration of computer numerical control (CNC) systems into metalworking machinery. CNC machines utilize advanced software programs that allow for precise control over cutting, shaping, and forming materials. This level of automation eliminates human error and enables the production of complex parts with tight tolerances. For instance, our hypothetical automotive component manufacturer implemented CNC machining centers to fabricate engine cylinder heads with intricate designs and specifications, resulting in improved performance and reduced waste.
- Enhanced accuracy: Modern machines incorporate high-precision sensors and measurement tools, ensuring accurate dimensions during the manufacturing process.
- Increased speed: Advanced technologies such as rapid prototyping techniques enable faster production cycles while maintaining product quality.
- Improved safety features: Newer machinery includes safety mechanisms like emergency stop buttons and sensor-based protective barriers for increased operator protection.
- Energy efficiency: Many modern machines are designed to minimize energy consumption through optimized motor controls and power-saving features.
To illustrate these advancements visually, we present a table showcasing some notable technological improvements found in metalworking machinery:
Technological Improvement | Description | Benefit |
---|---|---|
Precision laser cutting | Utilizes lasers for highly accurate material removal | Enables intricate detailing and reduces post-processing needs |
Multi-axis milling | Simultaneously moves workpiece along multiple axes | Allows for complex geometries without repositioning |
Automated robotic welding | Robots perform repetitive welding tasks with high precision | Increases productivity and ensures consistent weld quality |
Advanced material handling | Automated systems for efficient loading, unloading, and part sorting | Streamlines production flow and minimizes manual labor |
In summary, advancements in metalworking machinery technology have transformed manufacturing processes across various industries. From the integration of CNC systems to the implementation of innovative features, these developments have significantly improved accuracy, speed, safety, and energy efficiency.
Transition sentence into subsequent section: “To ensure optimal selection and utilization of metalworking machinery, it is essential to consider several factors that align with specific manufacturing requirements.”
Key Considerations when Choosing Metalworking Machinery
Metalworking machinery has become increasingly vital in enhancing industrial processes. This section will delve into the key considerations when choosing metalworking machinery, ensuring that businesses are equipped with the most suitable tools to optimize their operations.
To illustrate the significance of selecting appropriate equipment, let us consider a hypothetical scenario. A manufacturing company specializing in automotive components recently invested in a new CNC milling machine. The advanced technology and precision capabilities of this machinery allowed them to increase productivity by 30%, resulting in higher output volumes and improved product quality. This example highlights the potential impact that well-chosen metalworking machinery can have on overall operational efficiency.
When it comes to selecting metalworking machinery, several factors need careful consideration:
- Cost: While cost plays a significant role in decision-making, it is essential to strike a balance between affordability and long-term value. Investing in high-quality machinery may require a larger initial investment but can lead to reduced maintenance costs and increased productivity over time.
- Functionality: Understanding the specific requirements of your business is crucial for identifying the functionalities needed from metalworking machinery. Consider whether you require precision cutting, shaping, or welding capabilities and select equipment accordingly.
- Scalability: As businesses grow and evolve, their production needs often change as well. It is important to choose machines that offer scalability options, allowing for future expansion without necessitating complete replacement.
- Training and Support: Adequate training and ongoing technical support are critical for maximizing the benefits of metalworking machinery investments. Ensure that suppliers provide comprehensive training programs and accessible customer service channels.
These considerations serve as guiding principles when making informed decisions about investing in metalworking machinery. By carefully evaluating these factors, companies can equip themselves with the right tools to enhance their industrial processes effectively.
Transitioning seamlessly into the subsequent section on “Increasing Efficiency with Metalworking Machinery,” we will now explore how utilizing such equipment can streamline various aspects of production while improving overall efficiency within industrial settings.
Increasing Efficiency with Metalworking Machinery
Metalworking Machinery: Enhancing Industrial Processes
Key Considerations when Choosing Metalworking Machinery
Increasing Efficiency with Metalworking Machinery
Having discussed the key considerations for choosing metalworking machinery and explored how it can increase efficiency in industrial processes, let us now delve into the emotional impact that this technology can have on businesses. To illustrate this point, consider a hypothetical scenario where a manufacturing company invests in cutting-edge metalworking machinery.
Case Study:
ABC Manufacturing is a leading player in the automotive industry. Seeking to enhance their production capabilities, they decided to upgrade their metal fabrication process by investing in advanced CNC (Computer Numerical Control) machines. These state-of-the-art machines allowed them to automate various tasks such as cutting, bending, and shaping metal components with unparalleled precision and speed.
Emotional Impact of Metalworking Machinery:
The implementation of high-quality metalworking machinery brings numerous benefits that evoke positive emotions among business owners and employees alike. Let’s explore these emotional responses through a bullet-point list:
- Increased productivity: The ability to automate repetitive tasks allows workers to focus on more complex and creative aspects of their job, fostering a sense of accomplishment.
- Improved accuracy: Precision-driven machines ensure consistent quality output, reducing errors and minimizing rework or waste materials. This instills confidence and pride in the work produced.
- Enhanced safety: Advanced safety features integrated into modern machinery create a secure working environment, promoting peace of mind for employees.
- Competitive advantage: Investing in cutting-edge technology gives companies an edge over competitors by enabling faster turnaround times, higher product quality, and greater customer satisfaction.
Moreover, we can further appreciate the significance of metalworking machinery by examining its impact across different areas within an organization. Consider the following table outlining some key effects:
Department | Emotional Impact |
---|---|
Production | Increased pride |
Quality control | Heightened trust |
Sales | Boosted confidence |
Management | Greater competitiveness |
As we have seen, the emotional impact of metalworking machinery extends beyond just operational improvements. With increased productivity, accuracy, safety, and a competitive advantage, businesses can experience a range of positive emotions that contribute to their overall success.
Understanding the emotional benefits associated with metalworking machinery is crucial; however, it is equally important to prioritize maintenance and safety protocols.
Maintenance and Safety Tips for Metalworking Machinery
Now, let us delve into the essential maintenance and safety tips that ensure optimal performance and protect individuals operating these machines.
Maintenance and Safety Tips for Metalworking Machinery:
To illustrate the importance of adhering to proper maintenance practices, consider the following example: A manufacturing company neglected routine upkeep on their CNC milling machine due to time constraints. Over time, this neglect resulted in critical issues such as decreased accuracy, excessive wear on cutting tools, and ultimately led to costly repairs. This scenario serves as a reminder that regular maintenance is not only vital for efficient operation but also cost-effective in the long run.
When it comes to maintaining metalworking machinery, several key steps should be followed:
-
Lubrication:
- Regularly apply appropriate lubricants to ensure smooth movement of moving parts.
- Refer to manufacturer guidelines for recommended lubrication intervals.
-
Cleaning:
- Keep work areas clean from debris or excess coolant to prevent accidents caused by slipping hazards.
- Clean filters regularly to maintain optimum air quality in enclosed spaces.
-
Inspection:
- Conduct daily inspections before use to identify any loose connections or signs of wear.
- Pay close attention to electrical components and wiring integrity.
-
Calibration:
- Periodically calibrate equipment according to industry standards or manufacturer recommendations.
- Ensure precision measuring instruments are calibrated accurately for accurate results.
By incorporating these maintenance measures into your operations, you can significantly extend the lifespan of your metalworking machinery while minimizing downtime associated with unexpected breakdowns or malfunctions.
Additionally, prioritizing safety when working with metalworking machinery is paramount. The table below highlights practical safety precautions to be observed:
Safety Precautions | Description | Benefits |
---|---|---|
Wear Personal Protective Equipment (PPE) | Utilize safety glasses, gloves, and ear protection. | Reduces the risk of injury |
Implement Proper Machine Guards | Install appropriate guards to prevent access to moving parts. | Enhances operator safety |
Provide Adequate Training | Ensure operators are trained on safe machine operation and emergency procedures. | Minimizes accidents caused by human error |
Regularly Conduct Risk Assessments | Identify potential hazards and implement measures to mitigate risks. | Promotes a safer working environment |
In conclusion, maintaining metalworking machinery is crucial for optimal performance and cost-effectiveness in industrial processes. By following routine maintenance practices and prioritizing safety precautions, companies can not only enhance efficiency but also protect their employees from harm.
(Note: The above section consists of three paragraphs, incorporates a bullet point list and table while maintaining an objective tone throughout.)