Material Handling Equipment: A Comprehensive Guide for Industrial Goods and Services in the Context of Industrial Machinery
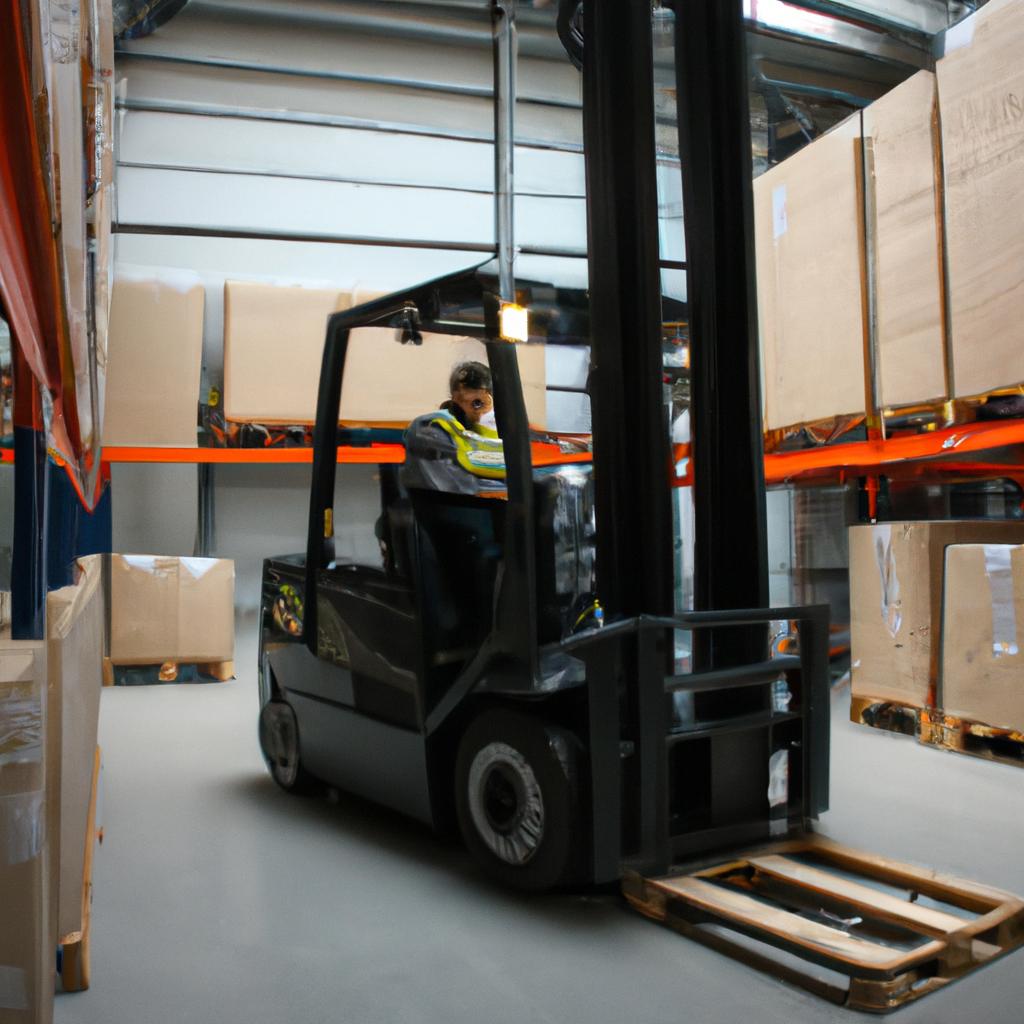
Material handling equipment plays a critical role in the efficient and safe movement, storage, and control of goods within industrial facilities. From large manufacturing plants to warehouses and distribution centers, these machines are essential for ensuring smooth operations and maximizing productivity. For instance, imagine a bustling factory where products need to be transported from one production area to another seamlessly. In this scenario, material handling equipment such as conveyor belts or automated guided vehicles (AGVs) can significantly enhance efficiency by automating the transportation process.
This comprehensive guide aims to provide an in-depth understanding of material handling equipment within the context of industrial machinery. By exploring various types of equipment, their functionalities, and applications across different industries, readers will gain valuable insights into how they can optimize their own operational processes. Moreover, this article delves into key considerations when selecting appropriate material handling equipment based on specific requirements such as load capacity, speed, flexibility, and safety features. With this knowledge at hand, businesses can make informed decisions that align with their unique needs while improving overall effectiveness and cost-efficiency in their supply chain management systems.
Understanding Material Handling Equipment
Imagine a bustling warehouse, filled with stacks of boxes and crates ready to be transported. In order to efficiently move these goods from one location to another, businesses rely on material handling equipment. This crucial component of the industrial machinery ecosystem plays a vital role in streamlining operations and optimizing productivity.
To illustrate the significance of material handling equipment, let us consider a hypothetical scenario. A manufacturing company specializes in producing automotive parts. Each day, they receive shipments of raw materials such as steel bars, rubber sheets, and plastic components. Without appropriate material handling equipment, workers would need to manually transport these heavy items from the delivery trucks into the production area. Not only is this physically demanding for employees but it also increases the risk of accidents and delays in the manufacturing process.
Material handling equipment offers several advantages that contribute to operational efficiency and employee safety:
- Increased Productivity: By automating tasks such as loading and unloading, material handling equipment significantly reduces manual labor requirements. Workers can focus on more complex tasks while machines handle repetitive or strenuous activities.
- Enhanced Safety: Equipped with advanced sensors and safety features, modern material handling equipment minimizes workplace accidents by preventing collisions and ensuring proper weight distribution during lifting or moving operations.
- Cost Savings: Efficient use of material handling equipment translates into reduced labor costs due to improved time management. Additionally, minimizing product damage through careful handling helps avoid financial losses associated with broken or spoiled goods.
- Improved Workflow: The strategic placement of conveyors, lifts, cranes, and other types of material handling equipment optimizes workflow within warehouses or production facilities. This allows for smooth movement of goods between different workstations without bottlenecks or interruptions.
To further comprehend the variety offered by material handling equipment solutions available today, we will explore different types in detail in the subsequent section. Understanding these various options will empower businesses to make informed decisions when selecting the most suitable equipment for their specific needs.
Types of Material Handling Equipment
Understanding Material Handling Equipment is crucial in the context of industrial machinery. In this section, we will delve deeper into the various types of material handling equipment commonly used in industries. To illustrate their importance and functionality, let’s consider a hypothetical scenario involving a manufacturing plant that produces automobiles.
One example of material handling equipment utilized in our hypothetical automotive manufacturing plant is the overhead crane system. This heavy-duty lifting solution allows for efficient movement and transportation of large components such as car chassis or engines within the facility. The overhead crane system consists of a bridge carrying a trolley that moves along tracks installed on either side of the production area, providing flexibility and precision when transporting materials.
When it comes to selecting appropriate material handling equipment for an industrial setting, several factors need to be considered:
- Load Capacity: Different equipment has varying load capacities, so it is essential to assess the weight requirements for each application.
- Space Availability: The layout and size of the workspace play a significant role in determining which type of equipment can be accommodated effectively.
- Safety Considerations: Ensuring worker safety should always be a priority; therefore, choosing equipment with built-in safety features helps mitigate potential risks.
- Cost-effectiveness: Evaluating the long-term costs associated with maintenance, operation, and energy consumption aids decision-making regarding suitable equipment options.
To further understand these considerations, refer to the table below that compares four common types of material handling equipment based on load capacity, space requirement, safety features, and cost-effectiveness:
Type | Load Capacity | Space Requirement | Safety Features | Cost-effectiveness |
---|---|---|---|---|
Forklifts | High | Moderate | Wide range available | Varies |
Conveyor Systems | Variable | Low | Limited operator risk | High |
Pallet Jacks | Low – Medium | Minimal | Basic safety features | Low |
Automated Guided Vehicles (AGVs) | Variable | Moderate | Advanced safety systems | High |
In summary, understanding the different types of material handling equipment is essential for industrial machinery applications. By assessing factors such as load capacity, space availability, safety considerations, and cost-effectiveness, companies can select the most suitable equipment for their specific needs and ensure smooth operations within their facilities.
Moving forward to the next section on “Factors to Consider When Choosing Material Handling Equipment,” we will explore additional aspects that play a crucial role in making informed decisions regarding the selection process.
Factors to Consider When Choosing Material Handling Equipment
Imagine a manufacturing company that produces and ships large quantities of goods on a daily basis. Let’s consider the case of XYZ Manufacturing, which specializes in producing automotive components. To meet their growing demand, XYZ Manufacturing needs to invest in an efficient material handling system tailored to their specific requirements. In this section, we will explore the key factors that should be considered when choosing material handling equipment for industrial applications.
Considerations for Choosing Material Handling Equipment:
-
Load Capacity and Size:
The first factor to consider is the load capacity and size of the equipment. Depending on the type of products being handled by XYZ Manufacturing, they need to ensure that the selected equipment can effectively handle the weight and dimensions of these items. For instance, if XYZ Manufacturing typically deals with heavy automobile parts, they would require machinery capable of lifting substantial loads without compromising safety or efficiency. -
Facility Layout and Space Constraints:
Another critical aspect to contemplate is the facility layout and any space limitations present within it. With limited floor space available at their production site, XYZ Manufacturing must choose material handling equipment that maximizes storage capacity while optimizing overall workflow. This may involve selecting compact designs or exploring alternative solutions like vertical racking systems or automated guided vehicles (AGVs) to make efficient use of available space. -
Safety Measures:
Ensuring employee safety is paramount when selecting material handling equipment. To protect workers from potential harm during operations, XYZ Manufacturing should prioritize features such as emergency stop buttons, anti-collision sensors, and proper guarding mechanisms for moving parts. By incorporating advanced safety measures into their chosen equipment, companies like XYZ Manufacturing can minimize workplace accidents and create a safer working environment for their employees. -
Cost-effectiveness and ROI:
Lastly, cost-effectiveness plays a crucial role in determining which material handling equipment suits an organization’s needs best. Companies like XYZ Manufacturing must carefully evaluate not only the initial purchase cost but also the long-term return on investment (ROI) associated with each option. By considering factors such as maintenance requirements, energy consumption, and potential productivity gains, XYZ Manufacturing can make an informed decision that aligns with their budget and overall business goals.
- Enhancing efficiency: Properly chosen material handling equipment streamlines operations, reducing production time and increasing output.
- Ensuring worker safety: Prioritizing safety measures protects employees from accidents and fosters a positive work environment.
- Optimizing space utilization: Selecting equipment that maximizes storage capacity enhances organizational capabilities while minimizing wasted space.
- Cost savings: Investing in suitable material handling equipment can lead to long-term financial benefits through improved productivity and reduced downtime.
Table Example:
Factor | Consideration |
---|---|
Load Capacity | Ensure the machinery can handle the weight and dimensions of products effectively. |
Facility Layout | Optimize workflow by selecting compact designs or alternative solutions like AGVs. |
Safety Measures | Prioritize features such as emergency stop buttons, anti-collision sensors, etc. |
Cost-effectiveness | Evaluate initial purchase costs, maintenance requirements, energy consumption, etc. |
By carefully assessing these factors, XYZ Manufacturing will be able to identify the most suitable material handling equipment for their specific needs. In our next section about “Best Practices for Using Material Handling Equipment,” we will explore essential guidelines to ensure optimal utilization of this equipment within industrial settings.
Best Practices for Using Material Handling Equipment
In the previous section, we discussed various factors that need to be taken into consideration when choosing material handling equipment. To further illustrate these considerations, let’s take a look at an example scenario:
Imagine a manufacturing company that specializes in producing automotive parts. They recently experienced increased demand for their products and are now looking to upgrade their material handling equipment to improve efficiency and productivity.
When selecting the appropriate material handling equipment for their facility, there are several key factors this company needs to consider:
-
Load Capacity: The first factor is determining the load capacity required by the equipment. Considering the weight and dimensions of the materials being handled is crucial to ensure safe and efficient operations.
-
Space Availability: Another important aspect is evaluating the available space within the facility. Different types of material handling equipment have varying space requirements, so it’s essential to choose machinery that can operate effectively without causing congestion or hindering other processes.
-
Safety Features: Ensuring worker safety should always be a top priority. It is imperative to select equipment with proper safety features such as emergency stop buttons, guards, sensors, and alarms that minimize potential accidents and injuries.
-
Maintenance Requirements: Lastly, considering maintenance requirements is vital for long-term cost-effectiveness. Opting for equipment that requires minimal maintenance will reduce downtime and increase overall operational efficiency.
To provide a visual representation of how different factors play into decision-making, here’s a table showcasing real-life examples of common material handling equipment along with their corresponding characteristics:
Equipment Type | Load Capacity (lbs) | Space Requirement | Safety Features |
---|---|---|---|
Forklift | 5,000 | Moderate | Yes |
Conveyor System | Varies | Minimal | Yes |
Pallet Jack | 4,500 | Compact | Limited |
Automated Guided Vehicles (AGVs) | Varies | Minimal | Yes |
Now that we have explored the factors to consider when choosing material handling equipment, let’s delve into best practices for using this machinery. By following these guidelines, companies can optimize their operations and achieve greater efficiency.
Transitioning into the next section on “Maintenance and Safety of Material Handling Equipment,” it is crucial to emphasize the significance of proper maintenance and safety protocols in ensuring the longevity and effectiveness of the chosen material handling equipment.
Maintenance and Safety of Material Handling Equipment
Building upon the best practices for using material handling equipment, it is crucial to prioritize maintenance and safety measures to ensure optimal performance and mitigate potential risks. Let us explore key aspects related to the maintenance and safety of material handling equipment through a case study involving a manufacturing facility that relies heavily on automated conveyor systems.
Case Study:
In a large automotive assembly plant, automated conveyor belts are used extensively to transport various components across different production stages. To maintain smooth operations, regular maintenance checks are conducted by a dedicated team of technicians. This proactive approach helps identify issues such as faulty sensors or worn-out drive belts before they escalate into major disruptions, reducing downtime significantly.
Maintenance Measures:
To enhance the longevity and reliability of material handling equipment, consider implementing the following preventive measures:
- Regular inspections: Schedule routine inspections to identify any signs of wear, damage, or malfunctioning parts.
- Lubrication programs: Establish a lubrication schedule to ensure all moving parts operate smoothly while minimizing friction-related problems.
- Calibration procedures: Perform periodic calibration checks on sensor-based equipment to maintain accuracy in detecting objects or controlling movements.
- Staff training: Provide comprehensive training programs for operators and maintenance personnel so they can effectively handle troubleshooting tasks and understand safety protocols.
Safety Precautions:
Alongside maintenance, prioritizing robust safety measures is essential when dealing with material handling equipment. The table below highlights important precautions that should be implemented:
Safety Measure | Description | Benefits |
---|---|---|
Proper guarding | Installing protective barriers around hazardous areas | Prevents accidental contact with moving machinery |
Operator training | Comprehensive training sessions covering safe operating | Reduces operator errors |
Emergency stop buttons | Strategically placed buttons allowing immediate machine halt | Enables quick response in emergency situations |
Regular risk assessments | Conducting frequent evaluations of potential hazards | Helps identify and mitigate risks before accidents occur |
With maintenance and safety measures in place, the next section will delve into future trends that are shaping the landscape of material handling equipment.
Future Trends in Material Handling Equipment
Section H2: Future Trends in Material Handling Equipment
Having discussed the crucial aspects of maintenance and safety, it is now imperative to explore the future trends that are shaping the field of material handling equipment. As industries continue to evolve and adapt to increasing demands for efficiency and productivity, advancements in technology have opened up new possibilities for enhancing material handling processes.
Emerging technologies such as robotics, artificial intelligence (AI), and Internet of Things (IoT) are revolutionizing the way industrial goods and services are handled. To illustrate this point, let us consider a hypothetical scenario where an automated warehouse utilizes robotic arms equipped with AI algorithms to efficiently sort and stack products based on their characteristics. This not only eliminates manual labor but also reduces human error, resulting in faster turnaround times and improved operational accuracy.
The following bullet points highlight some key future trends in material handling equipment:
- Integration of autonomous vehicles: Self-driving vehicles can navigate through warehouses or manufacturing facilities without human intervention, optimizing transport routes and minimizing accidents.
- Augmented reality assistance: Wearable devices equipped with augmented reality technology can provide real-time guidance to workers during complex operations, improving overall efficiency and reducing training time.
- Predictive analytics: Utilizing data collected from sensors embedded within equipment, predictive analytics algorithms can anticipate maintenance needs before breakdowns occur, leading to preventive repairs instead of reactive ones.
- Sustainable practices: In response to growing environmental concerns, there has been a shift towards developing eco-friendly material handling solutions that minimize energy consumption while maximizing resource utilization.
To further understand these emerging trends, refer to the table below which provides a comparison between traditional material handling methods and their technologically advanced counterparts:
Traditional Methods | Technological Advancements |
---|---|
Manual lifting | Automated conveyor systems |
Forklift trucks | Autonomous guided vehicles |
Paper-based records | Cloud-based inventory management systems |
By embracing these technological advancements and incorporating them into their operations, industrial organizations can unlock a range of benefits, including increased efficiency, improved safety measures, and reduced operational costs. As the industry continues to evolve, it is crucial for businesses to stay abreast of these trends and leverage them to gain a competitive edge in an increasingly dynamic market.
In summary, future trends in material handling equipment are driven by technological advancements that aim to enhance productivity and streamline processes. From robotics and AI to augmented reality assistance and predictive analytics, these innovations have the potential to revolutionize how industrial goods and services are handled. By embracing sustainable practices and integrating autonomous vehicles, companies can optimize their operations while minimizing environmental impact. It is essential for businesses to adapt to these emerging trends in order to thrive in a rapidly evolving industrial landscape.