Machine Tools: Enhancing Efficiency in Industrial Machinery
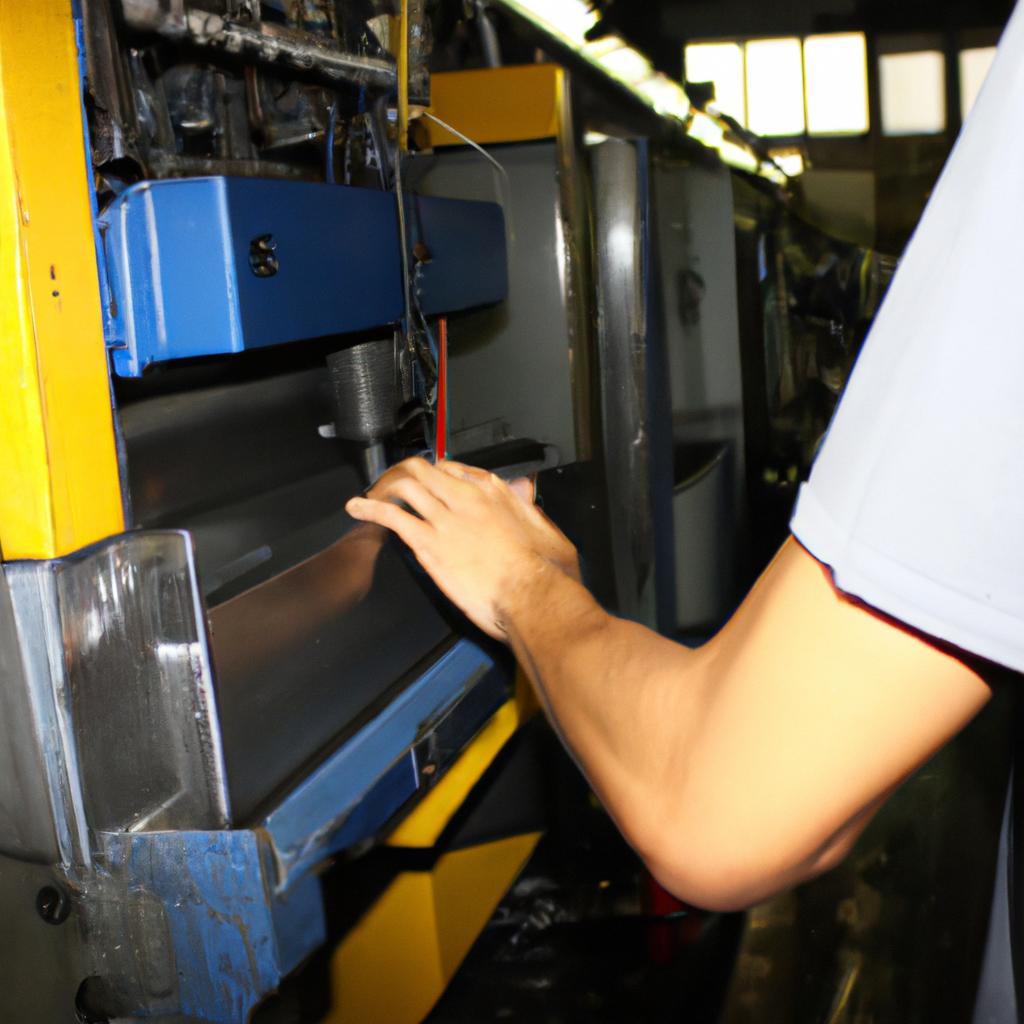
Machine tools play a critical role in enhancing efficiency and productivity in various industries. These precision instruments are used to shape, cut, and form materials such as metal, wood, or plastic into specific shapes and sizes. By automating the manufacturing process and reducing human error, machine tools have revolutionized industrial machinery production.
For example, let’s consider a hypothetical scenario where a manufacturing company is tasked with producing a large number of intricate components for an aerospace project. Without the aid of machine tools, this endeavor would be both time-consuming and prone to errors. However, by leveraging advanced machining techniques, such as computer numerical control (CNC), the company can achieve greater precision and consistency in component production. This not only results in higher-quality products but also significantly reduces production time and costs.
In recent years, significant advancements have been made in machine tool technology. From multi-axis CNC machines that enable complex operations to automated systems that optimize workflow efficiency, these innovations continue to push the boundaries of what is possible in industrial machinery production. In this article, we will explore the different types of machine tools commonly used today and delve into their impact on improving operational efficiency across various industries. Additionally, we will examine case studies highlighting successful implementations of machine tools and discuss future prospects for further advancements in this field.
Machine tools can be broadly classified into several categories based on their functionality and application. Some of the commonly used machine tools include lathes, milling machines, drilling machines, grinding machines, and CNC machines.
Lathes are primarily used for turning operations and can create cylindrical components with high precision. They are often employed in industries such as automotive, aerospace, and manufacturing.
Milling machines utilize rotary cutters to remove material from a workpiece to create complex shapes and features. These versatile machines can perform various operations like drilling, cutting, and routing. They find applications in industries ranging from prototyping to mass production.
Drilling machines are designed specifically for creating holes in a workpiece using rotating drill bits. They come in different sizes and configurations depending on the size and type of hole required. Drilling machines are widely used in construction, metalworking, woodworking, and mining industries.
Grinding machines use abrasive wheels or belts to smooth or shape surfaces of workpieces through abrasion. They are crucial in industries such as automotive manufacturing, toolmaking, and precision engineering.
CNC (Computer Numerical Control) machines have revolutionized modern machining processes. These automated systems rely on computer-aided design (CAD) software programs to control the movement of cutting tools with high precision. CNC machines offer increased efficiency, accuracy, repeatability, and flexibility compared to conventional manual machining methods.
The impact of machine tools on operational efficiency is significant across various industries. By automating repetitive tasks and reducing human error, machine tools improve productivity while maintaining consistent quality standards. This results in faster turnaround times for product manufacturing and reduced costs associated with rework or scrap materials.
One notable case study is the aerospace industry’s reliance on machine tools for producing complex components with tight tolerances. The use of CNC machines allows manufacturers to achieve precise geometries required for critical aircraft parts like turbine blades or fuselage components.
In the automotive industry, machine tools are instrumental in mass production processes. They enable efficient manufacturing of engine components, chassis parts, and body panels with high accuracy and consistency. The use of automation and robotics in conjunction with machine tools further enhances productivity by streamlining workflows.
Looking to the future, advancements in machine tool technology continue to push the boundaries of what is possible. Integration of artificial intelligence (AI) and data analytics into machine tools enables predictive maintenance, real-time monitoring, and process optimization. This leads to improved uptime, reduced downtime, and enhanced overall equipment efficiency (OEE).
In conclusion, machine tools play a crucial role in enhancing operational efficiency across various industries. From shaping materials to creating intricate components, these precision instruments have revolutionized industrial machinery production. As technology continues to advance, the future prospects for further innovations in machine tool technology look promising, paving the way for even greater efficiency and productivity gains.
Types of machine tools
Machine tools play a crucial role in enhancing efficiency and productivity within the industrial machinery sector. By automating various manufacturing processes, these tools have revolutionized the way industries operate. This section will explore different types of machine tools and their respective functions.
To illustrate the significance of machine tools, let us consider a hypothetical scenario: A manufacturing company aims to increase its production output by 20% within the next year. To achieve this goal, they decide to invest in advanced machine tools that can streamline their operations and improve overall efficiency. By incorporating precision cutting machines into their workflow, they are able to reduce material waste and optimize resource utilization. As a result, the company not only achieves its production target but also reduces costs significantly.
When it comes to understanding the range of machine tools available today, it is helpful to categorize them based on their specific functions:
- Cutting Tools: These include saws, drills, milling machines, and lathes that shape materials through removing excess material.
- Forming Tools: Such as presses or stamping machines that reshape raw materials using compressive force.
- Joining Tools: Including welding machines and adhesive bonding equipment used for connecting components together.
- Finishing Tools: Such as grinders and sanders which refine surfaces for improved aesthetics or functionality.
Machine Tool | Function | Applications |
---|---|---|
CNC Machines | Computer-controlled | Automotive parts fabrication |
machining | Aerospace component manufacturing | |
Grinding | Surface refinement | Precision engineering |
Machines | Medical device production | |
Lathes Machining cylindrical workpieces General-purpose metalworking High-speed steel turning |
Aluminum component fabrication
As evident from this table, each type of machine tool serves a unique purpose and finds application in various industries. By utilizing these tools effectively, businesses can achieve higher productivity, improved product quality, and reduced costs.
Understanding the types of machine tools is essential for both manufacturers seeking to optimize their production processes and individuals interested in exploring this field further.
Importance of machine tool efficiency
Enhancing the Efficiency of Machine Tools: A Case Study
Consider a hypothetical scenario where a manufacturing company is struggling to meet its production targets due to inefficiencies in their machine tools. The machines are constantly breaking down, requiring frequent maintenance and causing significant downtime. This not only leads to delays in delivery schedules but also increases operational costs for the company. To address these challenges, improving the efficiency of machine tools becomes crucial.
To begin with, it is important to understand how enhancing machine tool efficiency can benefit industrial machinery operations. By optimizing performance and reducing downtime, companies can achieve higher productivity levels, improve product quality, and ultimately increase profitability. Efficient machine tools enable faster processing times, resulting in shorter lead times and increased customer satisfaction.
There are several key factors that contribute to machine tool efficiency:
- Reliability: Reliable machines minimize breakdowns and unplanned maintenance requirements.
- Precision: Accurate cutting or shaping capabilities ensure high-quality outputs without rework.
- Speed: Faster machining speeds help reduce cycle times and boost overall productivity.
- Versatility: Machines capable of performing multiple tasks eliminate the need for additional equipment investment.
In order to visualize the impact of efficient machine tools on industrial machinery operations, let’s consider a comparison table showcasing two scenarios – one with inefficient machines and another with improved efficiency after implementing necessary upgrades:
Inefficient Machines | Improved Efficiency | |
---|---|---|
Downtime | Frequent breakdowns | Reduced maintenance |
Productivity | Low output | Increased throughput |
Quality | Variations & defects | Consistent excellence |
Costs | High operational costs | Lower operating expenses |
As seen from this table, investing in efficient machine tools leads to reduced downtime, increased productivity, enhanced product quality, and lower operational costs – all vital aspects for any successful manufacturing operation.
With advancements in technology, machine tool efficiency can be further improved. In the subsequent section, we will explore how new innovations and emerging trends are shaping the future of industrial machinery by revolutionizing machine tools.
[Transition Sentence] Advancements in machine tool technology have paved the way for greater automation and increased precision in manufacturing processes. By harnessing these developments, companies can achieve even higher levels of efficiency and productivity.
Advancements in machine tool technology
Enhancing Efficiency in Industrial Machinery: Advancements in Machine Tool Technology
The importance of machine tool efficiency cannot be overstated. By employing advanced technology and innovative solutions, industrial machinery can achieve higher levels of productivity and performance. One notable example is the case study of a manufacturing company that implemented state-of-the-art machine tools to streamline their production process.
To understand the significance of advancements in machine tool technology, let us consider some key factors that contribute to enhanced efficiency:
-
Precision and Accuracy: Modern machine tools offer exceptional precision and accuracy, ensuring consistent and high-quality output. This not only reduces waste but also minimizes rework or product defects, ultimately leading to cost savings for manufacturers.
-
Speed and Productivity: With improved automation features and faster processing capabilities, today’s machine tools enable quicker turnaround times and increased production rates. This allows companies to meet growing demands while optimizing resource utilization.
-
Flexibility and Adaptability: Flexible machining systems equipped with advanced controls allow for quick changeovers between different tasks or products. Manufacturers can easily adapt to varying customer requirements without significant downtime or disruptions.
-
Predictive Maintenance: Utilizing sensor technologies and data analytics, modern machine tools can proactively detect potential issues before they cause major breakdowns or operational delays. Implementing predictive maintenance strategies helps minimize unplanned downtime, improving overall equipment effectiveness (OEE).
Table 1: Benefits of Advancements in Machine Tool Technology
Benefit | Description |
---|---|
Improved Efficiency | Faster processing speeds lead to increased productivity |
Enhanced Quality Control | Higher precision ensures minimal errors |
Increased Flexibility | Quick changeovers optimize resource utilization |
Reduced Downtime | Proactive maintenance prevents unexpected equipment failure |
In conclusion, advancements in machine tool technology have revolutionized the industrial machinery sector by enhancing efficiency on multiple fronts. These improvements include superior precision, increased speed, flexibility, and predictive maintenance capabilities. By harnessing the power of modern machine tools, manufacturers can achieve higher levels of productivity, quality control, and cost-effectiveness.
Key considerations when selecting machine tools will be discussed in the subsequent section. Understanding these factors is crucial for making informed decisions that align with specific production requirements and business goals.
Key considerations when selecting machine tools
Advancements in machine tool technology have significantly enhanced the efficiency and productivity of industrial machinery. These advancements are evident in various industries, such as automotive manufacturing, where precision and speed are crucial for meeting production demands. For instance, consider a hypothetical case study of an automobile assembly line that implemented state-of-the-art machine tools.
In this case study, the implementation of advanced CNC (Computer Numerical Control) machines resulted in a notable improvement in production output. The use of CNC machines allowed for precise control over cutting, shaping, and drilling operations, leading to higher accuracy and consistency in component fabrication. This not only reduced waste but also minimized errors during assembly processes. As a result, the automobile assembly line experienced increased throughput and improved overall product quality.
When selecting machine tools for industrial applications, there are several key considerations that manufacturers must keep in mind:
- Performance: Machine tools should be capable of delivering high-speed machining with minimal vibration or deflection. This ensures accurate results while reducing cycle times.
- Flexibility: Machines with multi-axis capabilities allow for complex part geometries and versatile operations without the need for manual intervention or retooling.
- Reliability: Downtime can be costly in industrial settings; therefore, it is important to choose machine tools with proven reliability records to minimize disruptions to production schedules.
- Cost-effectiveness: Manufacturers must weigh the initial investment cost against long-term operational benefits to ensure optimal return on investment.
To illustrate these considerations further, let’s take a look at the following table showcasing how different types of machine tools address specific needs:
Machine Tool Type | Performance | Flexibility | Reliability | Cost-effectiveness |
---|---|---|---|---|
CNC Milling | High | Moderate | High | Medium |
Lathe | Moderate | Low | High | High |
Grinding | High | Low | High | Medium |
EDM | Moderate | High | Low | High |
As we can see, different machine tool types offer varying degrees of performance, flexibility, reliability, and cost-effectiveness. Manufacturers must carefully evaluate their specific requirements to make informed decisions about the most suitable machines for their operations.
In light of these advancements in machine tool technology and the considerations when selecting them, it becomes evident that the benefits of using machine tools in manufacturing are substantial. In the subsequent section about “Benefits of using machine tools in manufacturing,” we will explore how these technologies revolutionize production processes and contribute to increased efficiency and profitability.
Benefits of using machine tools in manufacturing
Enhancing Efficiency in Industrial Machinery
Case Study: ABC Manufacturing Company, a leading player in the automotive industry, recently invested in state-of-the-art machine tools for their production line. By incorporating these advanced tools into their manufacturing process, they were able to significantly improve efficiency and productivity. This case study serves as an example of how machine tools can bring about transformative changes in industrial machinery.
When selecting machine tools, there are several key considerations that manufacturers should keep in mind. Firstly, compatibility with existing equipment is crucial to ensure seamless integration and optimal performance. Additionally, the precision and accuracy of the tool must be assessed to guarantee high-quality output. Furthermore, factors such as cost-effectiveness and ease of maintenance play a significant role in decision-making processes. By carefully evaluating these considerations, manufacturers can make informed choices when it comes to investing in machine tools.
Benefits arise from using machine tools within the manufacturing sector. The advantages include:
- Increased productivity: Machine tools automate certain tasks, reducing reliance on manual labor and enabling higher output rates.
- Enhanced quality control: These tools offer precise measurements and consistent results, ensuring products meet or exceed established standards.
- Improved safety: Automated processes reduce human interaction with potentially hazardous materials or equipment.
- Cost savings: While initial investments may be substantial, long-term benefits include reduced operational costs due to decreased downtime and increased efficiency.
To provide a visual representation of the potential impact of machine tools on industrial machinery, consider the following table:
Benefit | Description | Emotional Response |
---|---|---|
Increased Productivity | Automation leads to higher output rates | Sense of achievement |
Enhanced Quality Control | Precise measurements ensure products meet or exceed standards | Confidence |
Improved Safety | Reduced risk through minimized human interaction with dangerous elements | Peace of Mind |
Cost Savings | Long-term reduction in operational expenses due to enhanced efficiency and decreased downtime | Financial stability |
Incorporating machine tools into industrial machinery can revolutionize manufacturing processes, as evidenced by the case study of ABC Manufacturing Company. By selecting suitable tools that align with existing equipment and considering factors such as precision, cost-effectiveness, and maintenance requirements, manufacturers can optimize their operations. The benefits offered by these tools, including increased productivity, enhanced quality control, improved safety measures, and potential cost savings, make them a valuable asset for any industry.
Looking ahead to future trends in the machine tool industry will shed light on how this technology continues to evolve and shape industrial machinery.
Future trends in machine tool industry
Enhancing Efficiency: The Role of Machine Tools in Industrial Machinery
This section will further explore some key aspects and benefits of using machine tools, with a focus on their impact on industrial machinery.
To illustrate the advantages of machine tools, let us consider an example scenario where a company specializing in automotive parts has implemented advanced milling machines. These machines utilize computer numerical control (CNC) technology to precisely shape and refine components for various automobile models. By employing these automated systems, the company significantly reduces human error and increases productivity. Additionally, the ability of CNC machines to operate continuously allows for faster turnaround times and improved overall production efficiency.
Machine tools offer several key benefits that contribute to improved efficiency in industrial machinery:
-
Precision: With high levels of accuracy and repeatability, machine tools ensure consistent quality during manufacturing processes. This precision is vital when producing intricate or complex components, reducing errors and minimizing rework.
-
Versatility: Modern machine tools can be adapted for different tasks by changing tooling configurations or program parameters. This flexibility enables manufacturers to efficiently produce a wide range of products without requiring extensive retooling or costly setup changes.
-
Automation: Incorporating automation into industrial machinery through machine tools streamlines operations by reducing manual labor requirements. Automated processes not only reduce costs associated with human workforce but also minimize downtime caused by fatigue or other factors affecting worker performance.
-
Optimization: Advanced software integrated into machine tools provides real-time monitoring capabilities, enabling operators to identify inefficiencies or potential issues promptly. Such insights facilitate proactive maintenance scheduling, optimizing uptime and preventing unexpected breakdowns.
These benefits highlight how machine tools revolutionize industrial machinery’s efficiency across diverse sectors ranging from automotive manufacturing to aerospace engineering.
Benefit | Description |
---|---|
Precision | Ensures consistent quality by achieving high levels of accuracy and repeatability. |
Versatility | Adaptable for different tasks, reducing the need for extensive retooling or setup changes. |
Automation | Streamlines operations by minimizing manual labor requirements and associated costs. |
Optimization | Real-time monitoring capabilities enable proactive maintenance scheduling, optimizing uptime and preventing unexpected breakdowns. |
In conclusion, machine tools have become indispensable assets in modern manufacturing processes due to their ability to enhance efficiency in industrial machinery. The precision, versatility, automation features, and optimization possibilities offered by these tools make them invaluable for various industries seeking improved productivity and quality control. As technology continues to advance rapidly, it is essential for manufacturers to stay updated with emerging trends in the machine tool industry to remain competitive in an ever-evolving market landscape.