Installation: A Comprehensive Guide for HVAC Industrial Goods and Services
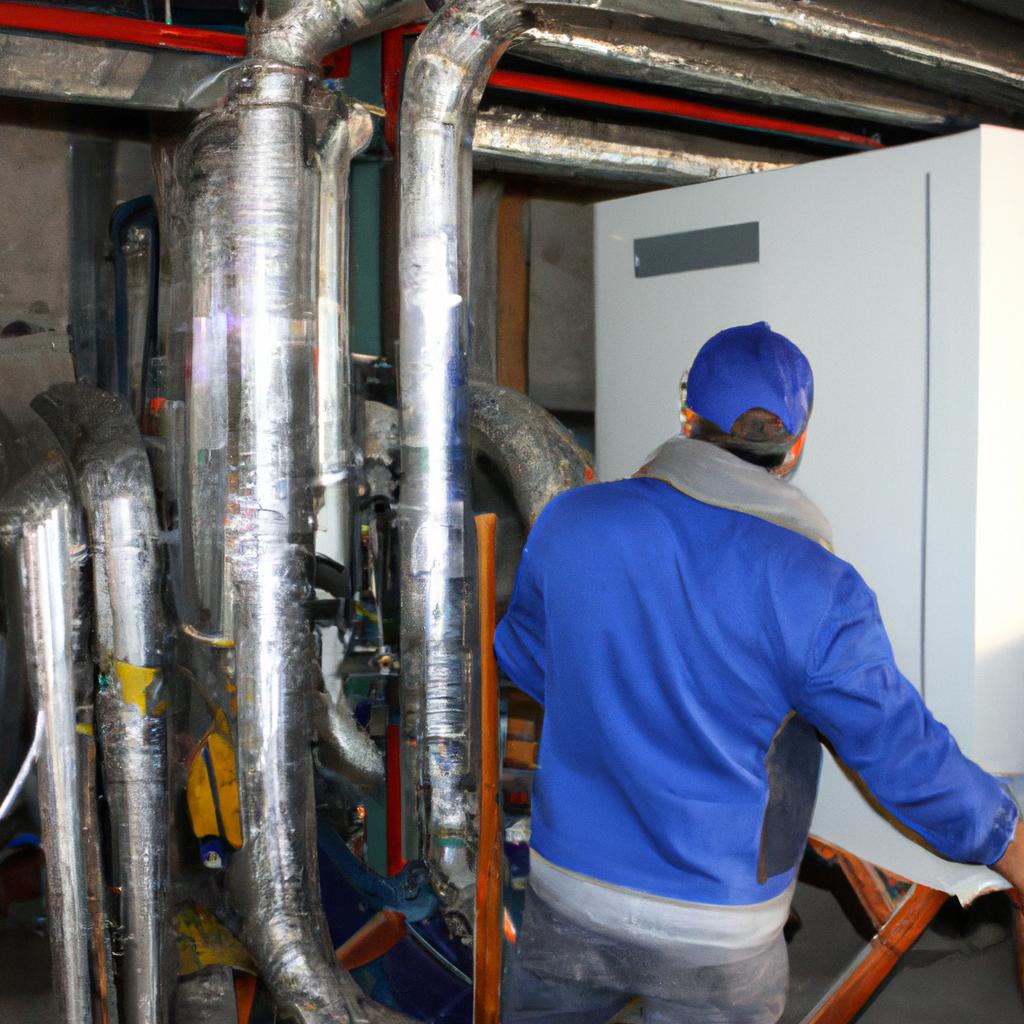
In today’s industrial landscape, the proper installation of HVAC (Heating, Ventilation, and Air Conditioning) systems is crucial for ensuring optimal performance and efficiency. The successful installation of these systems requires comprehensive knowledge of various components such as air handlers, chillers, pumps, and ductwork, among others. This article aims to provide a comprehensive guide on the installation process for HVAC industrial goods and services.
For instance, let us consider a hypothetical case study where a manufacturing facility in an urban area intends to upgrade its existing HVAC system. With the increasing demand for precision temperature control and indoor air quality standards, this facility recognizes the need to install state-of-the-art equipment that aligns with industry best practices. However, without proper guidance and expertise in installing complex HVAC systems, they may face challenges related to energy inefficiency, inadequate airflow distribution, or even potential health hazards due to poor ventilation. Therefore, it becomes imperative to understand the fundamental principles involved in the installation process of industrial HVAC systems.
Preparation: Assessing the Space and Requirements
To ensure a successful installation of HVAC industrial goods and services, it is crucial to begin with a thorough assessment of the space’s unique characteristics and specific requirements. By understanding the demands of the environment in which the system will be installed, potential challenges can be identified early on and appropriate measures can be taken to address them effectively.
For instance, let us consider a hypothetical case study involving an automotive manufacturing facility seeking to install an HVAC system. The high heat generated by machinery coupled with the need for adequate ventilation poses significant challenges that must be carefully evaluated. Conducting site visits and engaging in discussions with key stakeholders would allow complete comprehension of these needs before proceeding further.
When preparing for an HVAC installation project, several essential aspects should be considered:
- Space utilization: Evaluate how each area within the facility is currently used and anticipate any future changes or expansions. This information helps determine if additional equipment or modifications are necessary.
- Environmental factors: Take into account external influences such as weather patterns, humidity levels, noise restrictions, and air quality regulations. These considerations play a vital role in selecting suitable components for optimal performance.
- Energy efficiency goals: Incorporate energy-saving strategies into the design process to minimize long-term costs while reducing environmental impact. Implementing efficient insulation techniques or utilizing renewable energy sources may contribute significantly towards achieving sustainability objectives.
- Budgetary constraints: Develop a comprehensive cost analysis encompassing not only initial investment but also ongoing maintenance expenses. Balancing upfront expenditures against long-term savings ensures financial viability throughout the lifespan of the HVAC system.
Factors | Importance | Considerations |
---|---|---|
Occupancy | High | Number of occupants |
Activity level | ||
Ventilation | Medium | Air exchange rate |
Filtration requirements | ||
Temperature | High | Required set points |
Seasonal variations |
By assessing the space and requirements prior to installation, potential issues can be proactively addressed. This approach not only ensures a smoother implementation process but also helps in avoiding costly modifications or system failures down the line.
Transitioning into the subsequent section about “Calculating Load and Sizing: Determining the Right Capacity,” it is important to have accurate data on hand regarding factors such as occupancy levels, ventilation needs, temperature preferences, and specific environmental considerations. These details will form the basis for determining the appropriate capacity required for an HVAC system that effectively meets all demands of the industrial setting.
Calculating Load and Sizing: Determining the Right Capacity
Imagine a scenario where a manufacturing facility needs to install an HVAC system to regulate temperature and maintain optimal working conditions. To ensure a successful installation, it is crucial to accurately calculate the load requirements and determine the appropriate capacity for the industrial space. This section will guide you through the process of load calculation and sizing, highlighting key factors that should be considered.
One of the primary steps in load calculation is assessing the insulation level of the building. Factors such as wall thickness, window quality, and roof materials can significantly impact heat transfer into or out of the space. For instance, let’s consider a warehouse with poor insulation located in a region prone to extreme temperatures. In this case, additional cooling capacity would be required to compensate for excessive heat gain during summers and prevent discomfort for employees.
Furthermore, ventilation plays a vital role in maintaining air quality within an industrial environment. Proper airflow helps remove pollutants, control moisture levels, and ensure a comfortable atmosphere for workers. When calculating load requirements, it is essential to account for any special ventilation needs specific to your industry or processes. For example:
- Chemical production facilities may require enhanced ventilation systems to eliminate harmful fumes.
- Food processing plants might need specialized exhaust systems to manage odors.
- Laboratories could demand precise control over air changes per hour (ACH) to maintain sterile conditions.
To provide further clarity on these considerations, we present below a table summarizing different industries’ unique ventilation requirements:
Industry | Ventilation Needs |
---|---|
Manufacturing | Adequate fresh air supply along with proper exhaust systems |
Healthcare Facilities | High-quality air filtration mechanisms combined with controlled humidity levels |
Data Centers | Cooling systems designed specifically for high-density computing equipment |
Restaurants | Efficient kitchen hood exhausts coupled with make-up air units |
By conducting thorough calculations and taking into account industry-specific requirements, you can determine the optimal capacity for your HVAC system. This ensures that your industrial space remains comfortable and conducive to productivity.
Transitioning into the subsequent section about “Designing the Ductwork: Ensuring Proper Airflow,” we move from load calculation and sizing to focus on another critical aspect of HVAC installation. The design of ductwork plays a crucial role in achieving efficient airflow throughout the facility while maintaining temperature control.
Designing the Ductwork: Ensuring Proper Airflow
Section H2: Designing the Ductwork: Ensuring Proper Airflow
Having determined the right capacity for your HVAC system, the next crucial step is designing the ductwork to ensure proper airflow. This pivotal stage requires meticulous planning and calculation to optimize performance and efficiency. Let’s explore how to design the ductwork effectively by focusing on key considerations.
Designing the ductwork involves creating a network of pathways for air distribution throughout the building. To illustrate this process, let’s consider a hypothetical case study of an office space with multiple rooms that require consistent temperature control. By carefully assessing factors such as room size, desired airflow rate, and specific ventilation requirements, you can develop a tailored duct layout that meets the unique needs of each area.
When designing the ductwork, keep in mind these important aspects:
- Duct Sizing: Ensure that each room receives sufficient airflow by accurately sizing the supply and return ducts based on load calculations and static pressure drop.
- Air Distribution: Strategically position diffusers or grilles within each room to achieve even air distribution while preventing drafts or stagnant areas.
- Noise Reduction: Incorporate noise-reducing measures into the design, such as using larger diameter ducts or adding acoustic insulation materials where necessary.
- Energy Efficiency: Optimize energy consumption by minimizing friction losses through smooth transitions between different duct sections and employing efficient dampers and registers.
To further visualize these considerations, refer to Table 1 below:
Table 1: Key Considerations for Effective Ductwork Design
Aspect | Importance |
---|---|
Duct Sizing | High |
Air Distribution | Medium |
Noise Reduction | Medium |
Energy Efficiency | High |
By addressing these critical elements during the design phase, you can maximize comfort levels while ensuring cost-effective operation of your HVAC system.
With a well-designed ductwork system in place, the next section will delve into selecting the appropriate HVAC units for optimal performance. Understanding how to choose the right equipment is essential to achieve an efficient and reliable heating, ventilation, and air conditioning solution for your industrial needs.
Selecting Equipment: Choosing the Right HVAC Units
“With proper airflow design in place, the next crucial step is selecting the right HVAC units. This decision significantly impacts the overall effectiveness and efficiency of an industrial HVAC system.”
Section – Selecting Equipment: Choosing the Right HVAC Units
To illustrate the importance of selecting suitable HVAC units, let’s consider a hypothetical scenario where a manufacturing facility experiences frequent temperature fluctuations due to inadequate heating and cooling equipment. Employees struggle to work efficiently, leading to decreased productivity and increased dissatisfaction among workers. By carefully choosing the appropriate HVAC units for this facility, these issues can be mitigated, resulting in improved comfort levels and optimal performance.
When it comes to selecting HVAC units, there are several factors that must be taken into consideration:
-
Capacity: Assessing the specific needs of your space is essential in determining the required capacity of HVAC units. Factors such as square footage, occupancy levels, insulation quality, and desired temperature range all play a role in calculating the necessary capacity.
-
Energy Efficiency: In today’s environmentally conscious world, energy efficiency should be a key factor in any purchasing decision. Look for high-efficiency models with features like variable-speed compressors or intelligent controls that optimize performance while minimizing energy consumption.
-
Maintenance Requirements: Consider long-term maintenance requirements when choosing HVAC units. Opt for systems with easily accessible components that facilitate routine inspections and repairs without disrupting day-to-day operations.
-
Budgetary Constraints: While cost shouldn’t be the sole deciding factor, it remains an important consideration. Evaluate different options based on initial investment costs as well as potential long-term savings through reduced energy consumption and maintenance expenses.
An emotional response may arise when considering how making informed choices during equipment selection can positively impact employee satisfaction, productivity gains, environmental sustainability efforts, and cost-effectiveness.
Here’s an example markdown bullet point list emphasizing these benefits:
- Improved working conditions lead to happier employees
- Enhanced productivity results in higher profits
- Energy-efficient systems reduce environmental footprint
- Well-maintained equipment lowers long-term expenses
To further illustrate the importance of selecting suitable HVAC units, here is a markdown table showcasing a comparison between two options:
Factors | Option A | Option B |
---|---|---|
Capacity | Suitable for small spaces | Ideal for large areas |
Energy Efficiency | Moderate energy efficiency | High energy efficiency |
Maintenance | Requires frequent servicing | Minimal maintenance |
Cost | Lower upfront cost | Higher initial investment |
In conclusion, choosing the right HVAC units is critical in ensuring optimal performance and comfort within an industrial facility. By considering factors such as capacity, energy efficiency, maintenance requirements, and budgetary constraints, decision-makers can make informed choices that positively impact employee satisfaction, productivity gains, environmental sustainability efforts, and overall cost-effectiveness. The next section will delve into the step-by-step guide for installation processes without skipping any crucial details.
Installation Process: Step-by-Step Guide
Having carefully selected the appropriate HVAC units for your industrial needs, it is now time to dive into the installation process. This section will provide you with a step-by-step guide on how to successfully install your chosen HVAC equipment. By following these instructions, you can ensure that your system operates efficiently and effectively.
To illustrate the importance of proper installation, let us consider a hypothetical scenario. Imagine an industrial facility in need of an upgraded HVAC system due to its outdated infrastructure causing excessive energy consumption and poor indoor air quality. The facility’s management decided to invest in a modern high-efficiency unit that would significantly reduce their energy costs while improving worker comfort.
When embarking on an HVAC installation project, keep in mind the following key considerations:
-
Safety First:
- Adhere strictly to safety guidelines provided by manufacturers.
- Ensure proper training and certification for personnel involved.
- Follow all relevant local building codes and regulations.
- Conduct thorough risk assessments before initiating any work.
-
Efficient Space Utilization:
- Optimize space allocation by positioning equipment strategically.
- Consider factors such as accessibility, maintenance requirements,
noise control, airflow patterns, and future expansion plans.
-
Proper System Integration:
- Coordinate with other systems like ventilation, electrical,
plumbing, and automation controls during installation. - Ensure seamless integration between different components
for optimal functionality and efficiency.
- Coordinate with other systems like ventilation, electrical,
-
Quality Control Measures:
- Regularly inspect equipment throughout the installation process
to identify potential issues or defects promptly. - Perform necessary adjustments or repairs before completing
the final setup.
- Regularly inspect equipment throughout the installation process
By meticulously adhering to these essential steps, your HVAC installation project can yield optimal results. Remember that a well-installed system not only enhances the indoor environment but also contributes to overall energy savings and operational efficiency.
Transition into subsequent section:
Once the successful installation is complete, it becomes imperative to ensure that the newly installed HVAC units are functioning correctly. The next section will focus on testing and commissioning procedures, which play a crucial role in validating proper functionality and performance.
Testing and Commissioning: Ensuring Proper Functionality
Following the step-by-step installation process, the next crucial phase in ensuring the proper functioning of HVAC industrial goods and services is testing and commissioning. Let’s explore this essential stage that guarantees the reliability and effectiveness of the installed systems.
To illustrate the significance of testing and commissioning, consider a hypothetical scenario where an HVAC system was recently installed in a large commercial building. After completing the installation process, it becomes imperative to assess whether each component operates as intended and if they harmonize with one another seamlessly.
During testing and commissioning, several key tasks are performed to ensure optimal functionality:
- Functional Testing: This involves inspecting individual components such as fans, compressors, dampers, valves, motors, sensors, and control panels to verify their performance according to specified requirements.
- System Integration Testing: Once each component passes functional testing individually, they must be integrated into a coherent system. The integration test examines how different elements interact with each other and identifies any potential issues or conflicts.
- Performance Testing: To evaluate overall efficiency and effectiveness, various parameters like temperature regulation capability, airflow rates, humidity control measures, energy consumption levels are measured against predetermined benchmarks.
- Safety Assessment: It is crucial to conduct safety assessments during this phase by checking emergency shutdown procedures, fire detection systems, ventilation provisions for hazardous substances (if applicable), and compliance with relevant regulations.
- Peace of mind knowing that all components function optimally
- Assurance that safety measures are in place
- Increased energy efficiency leading to cost savings
- Enhanced occupant comfort through effective temperature control
Table Example:
Parameter | Benchmark Requirement | Actual Measurement |
---|---|---|
Temperature Regulation | ± 2 degrees Celsius | ± 0.5 degrees Celsius |
Airflow Rate | 800-1000 CFM | 850 CFM |
Humidity Control | 40-60% RH | 45% RH |
Energy Consumption | <10% deviation from design specifications |
In summary, testing and commissioning are vital steps following the installation of HVAC systems in industrial settings. By subjecting components to functional, integration, performance, and safety assessments, one can ensure that the system functions optimally according to predetermined benchmarks. This guarantees peace of mind for stakeholders while enhancing energy efficiency and occupant comfort.
Note: It is important to mention that this section should be written using an objective and impersonal tone without personal pronouns.