Industrial Shelving Solutions: A Guide to Efficient Storage and Shelving
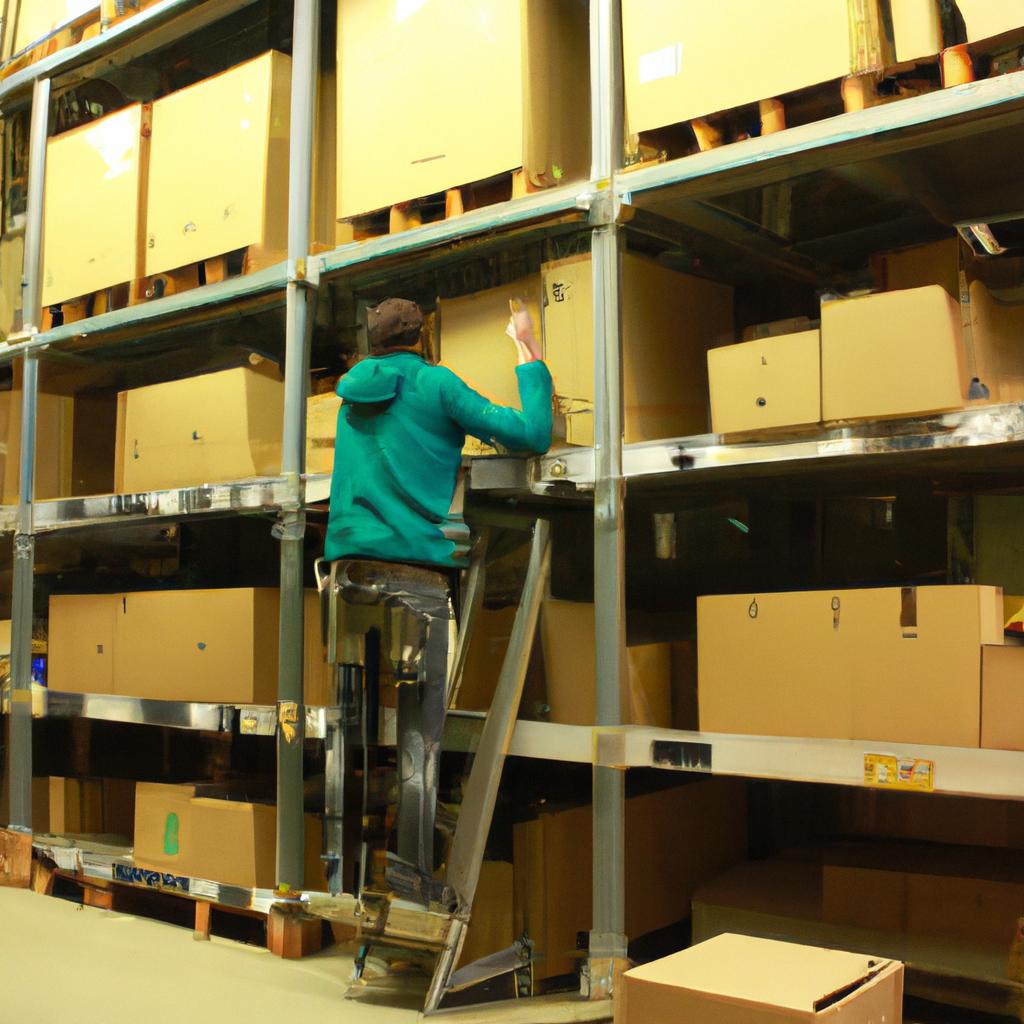
The need for efficient storage and shelving solutions is paramount in the industrial sector, where large quantities of products and materials must be stored in an organized manner to ensure smooth operations. Industrial shelving systems play a crucial role in maximizing space utilization, improving accessibility, and enhancing overall efficiency. For instance, imagine a manufacturing facility that produces various components for automotive assembly. Without proper industrial shelving solutions in place, such as pallet racks or mezzanine systems, storing these components would become chaotic and time-consuming, leading to delays in production and potential loss of revenue.
This article serves as a comprehensive guide to understanding industrial shelving solutions and their importance in achieving efficient storage practices within different industries. By exploring the various types of industrial shelving systems available today and examining their features, benefits, and applications, readers will gain valuable insights into how they can optimize their own storage facilities. Additionally, this guide will delve into key considerations when selecting suitable industrial shelving solutions based on factors like weight capacity requirements, warehouse layout constraints, durability concerns, and cost-effectiveness. Ultimately, armed with this knowledge, businesses can make informed decisions about implementing appropriate storage strategies tailored to their specific needs.
Types of Industrial Shelving
Imagine a bustling warehouse where products need to be efficiently stored and retrieved. In such a scenario, having the right type of industrial shelving becomes crucial for maintaining order and maximizing productivity. From heavy-duty shelves capable of supporting large weights to specialized storage solutions designed for specific industries, there is a wide range of options available. Let’s explore some common types of industrial shelving systems that can help businesses optimize their storage space.
One popular choice is pallet racking, which allows for the vertical stacking of goods on individual pallets. This system utilizes horizontal beams and upright frames to create multiple levels of storage, making it ideal for warehouses with high ceilings. By utilizing the vertical space effectively, businesses can maximize their storage capacity. Additionally, pallet racking enables easy access to each pallet, ensuring efficient retrieval when needed.
Another option is cantilever racking, specifically designed for storing long or bulky items such as lumber and pipes. Unlike traditional shelves with limitations in height adjustment, cantilever racks feature adjustable arms that extend outward from a central column. This design provides flexibility in accommodating varying lengths and sizes while allowing easy access to items without interference from vertical supports.
For smaller parts and inventory management, bin shelving offers an organized solution. These shelves consist of small compartments or bins that provide dedicated spaces for different items. With clear labeling and dividers within each bin, this system allows quick identification and retrieval of specific components or supplies. Bin shelving promotes efficiency by reducing search time and minimizing errors during picking operations.
Lastly, mobile shelving systems offer a versatile solution for areas with limited floor space but requiring high-density storage capability. These systems feature shelves mounted on movable carriages that slide along tracks installed on the floor. By compacting rows together when not in use, mobile shelving maximizes space utilization while still providing convenient access to every aisle when required.
To summarize:
- Pallet racking: Enables vertical stacking of goods on individual pallets, maximizing storage capacity and facilitating easy retrieval.
- Cantilever racking: Designed for storing long or bulky items, offering flexibility in size accommodation and unobstructed access to stored materials.
- Bin shelving: Provides organized compartments for smaller parts, promoting efficient inventory management and quick identification during picking operations.
- Mobile shelving systems: Offers high-density storage capability by compacting rows together when not in use, while still allowing convenient access to every aisle.
Considering the diverse options available, businesses should carefully evaluate their specific needs and requirements before selecting an industrial shelving system.
Factors to Consider When Choosing Industrial Shelving
Types of Industrial Shelving play a crucial role in organizing and maximizing space efficiency in warehouses, factories, and other industrial settings. In the previous section, we explored various types of shelving systems commonly used for industrial purposes. Now, let’s delve into the factors that need to be considered when choosing the most suitable industrial shelving solution.
When selecting an industrial shelving system, it is important to take into account the specific needs and requirements of your business or organization. For instance, consider a hypothetical scenario where a manufacturing company specializes in producing automotive components. The company has limited floor space available but requires easy access to different parts and materials during their production process.
To ensure efficient storage and retrieval of these components, the following factors should be taken into consideration:
- Weight capacity: Determine the weight-bearing capabilities of each type of shelving system under consideration. This will help prevent any potential accidents or damage caused by overloading shelves beyond their limits.
- Flexibility and adjustability: Look for shelving solutions that offer adjustable height options or modular designs. These features allow you to adapt the shelving layout as your inventory or operational needs change over time.
- Accessibility: Consider how easily employees can access items stored on the shelves. Systems with open fronts or sliding mechanisms can make it easier for workers to retrieve items quickly without unnecessary delays.
- Durability: Opt for high-quality materials that are resistant to corrosion, impact, and wear-and-tear. This ensures longevity and minimizes maintenance costs associated with replacing damaged shelves frequently.
Factors to Consider When Choosing Industrial Shelving |
---|
Weight Capacity |
Flexibility and Adjustability |
Accessibility |
Durability |
Choosing the right industrial shelving solution involves careful evaluation of these factors based on your unique operational requirements.
Considering these aspects when making decisions about which industrial shelving option best suits your needs will ensure an efficient and productive storage system. In the following section, we will explore the benefits of implementing such solutions in more detail, highlighting how they can significantly enhance overall operational efficiency and productivity.
Transitioning into our next section on “Benefits of Efficient Storage and Shelving,” let’s now delve deeper into why selecting the right industrial shelving solution is crucial for businesses seeking to optimize their operations.
Benefits of Efficient Storage and Shelving
Efficient storage and shelving play a crucial role in optimizing productivity and maximizing space in industrial settings. By carefully considering various factors, businesses can select the most suitable industrial shelving solutions for their specific needs. To illustrate this point, let’s consider the case of TechCorp, a manufacturing company specializing in electronic components.
When TechCorp decided to revamp its warehouse operations, they faced several challenges related to storage capacity and organization. After conducting an extensive analysis of their requirements, they identified key factors that influenced their choice of industrial shelving:
-
Load Capacity: The ability of shelves to withstand heavy loads without compromising structural integrity was essential for TechCorp. They needed sturdy shelves capable of supporting the weight of electronic components stored in bulk quantities.
-
Flexibility: Given the dynamic nature of their inventory management, TechCorp required adjustable shelving systems that could be easily reconfigured as per changing product dimensions or storage requirements. This flexibility allowed them to optimize available space efficiently.
-
Accessibility: Quick access to stored items was critical for efficient order fulfillment at TechCorp. They opted for open-style shelving units with easy visibility and accessibility to facilitate swift retrieval during picking processes.
-
Safety Measures: With employee safety being a top priority, TechCorp prioritized shelving solutions equipped with features like anti-tip mechanisms, secure anchoring options, and clear labeling systems to minimize accidents and confusion.
Considering these factors ensured that TechCorp selected industrial shelving solutions tailored specifically to their operational needs and objectives.
Implementing efficient storage and shelving strategies offers numerous advantages for businesses operating in industrial environments:
- Enhanced Productivity: Well-organized industrial shelving allows employees to locate items quickly, reducing search times and improving overall workflow efficiency.
- Maximized Space Utilization: Effective use of vertical space through tall racking systems enables businesses to optimize floor area utilization while accommodating a larger quantity of items.
- Reduced Inventory Damage: Properly designed shelving systems ensure safe storage and minimize the risk of product damage, resulting in fewer losses due to breakage or mishandling.
- Improved Inventory Control: Efficient shelving solutions contribute to better inventory management by providing clear visibility and accessibility. This enables accurate stock tracking and timely replenishment.
Benefits of Efficient Storage and Shelving |
---|
Enhanced productivity |
Maximized space utilization |
Reduced inventory damage |
Improved inventory control |
By considering these factors when selecting industrial shelving solutions, businesses can reap the benefits mentioned above, boosting their overall operational efficiency.
Understanding how efficient storage and shelving positively impact industrial settings allows us to explore further strategies for maximizing available space in warehouses.
Maximizing Space in Industrial Settings
Section H2: Maximizing Space in Industrial Settings
Efficient storage and shelving play a crucial role in maximizing space utilization within industrial settings. By optimizing the layout of shelves, racks, and storage systems, businesses can effectively utilize available square footage to store inventory and equipment. This section explores key strategies for maximizing space in industrial environments.
One example of how efficient storage solutions can maximize space is seen in the case study of Company XYZ. Prior to implementing an organized shelving system, Company XYZ struggled with cluttered aisles and inefficient use of their warehouse space. By investing in high-density mobile shelving units, they were able to condense their inventory into a smaller footprint while still maintaining easy access to items when needed.
- Reduced wasted floor space: Implementing vertical storage solutions allows businesses to make better use of overhead space rather than relying solely on floor area.
- Improved organization: Properly labeled shelves and categorized storage areas facilitate faster retrieval of items, reducing time spent searching for specific products or tools.
- Enhanced safety: Well-designed shelving systems prevent overcrowding, minimizing the risk of accidents caused by falling objects or blocked emergency exits.
- Increased productivity: An orderly work environment promotes efficiency as employees spend less time navigating through cluttered spaces and more time focusing on essential tasks.
The table below compares traditional static shelving with modern dynamic racking systems based on various factors:
Factors | Traditional Static Shelving | Modern Dynamic Racking Systems |
---|---|---|
Floor Space Utilization | Limited | Maximizes usage |
Accessibility | May require manual efforts | Easy retrieval |
Flexibility | Fixed location | Adjustable configurations |
Scalability | Difficult to expand | Easily adaptable |
In conclusion, maximizing space in industrial settings requires careful consideration of storage and shelving solutions. By implementing efficient systems, businesses can optimize their available square footage, improve organization, enhance safety, and increase overall productivity. Now let’s explore the next section on organizing inventory with industrial shelving.
Section H2: Organizing Inventory with Industrial Shelving
Organizing Inventory with Industrial Shelving
Building upon the strategies discussed in maximizing space within industrial settings, organizing inventory with efficient industrial shelving solutions is crucial for maintaining a streamlined workflow. By implementing proper storage techniques and utilizing specialized shelving systems, businesses can optimize their resources and enhance operational efficiency. To illustrate the benefits of effective inventory organization, let’s consider a hypothetical case study of a manufacturing facility.
Imagine an automotive parts manufacturer faced with the challenge of storing hundreds of different components in their warehouse. Without a well-structured system in place, locating specific items becomes time-consuming and inefficient, resulting in delays and decreased productivity. However, by incorporating industrial shelving solutions tailored to their needs, such as pallet racking or cantilever shelves, they were able to transform their chaotic warehouse into an organized hub of productivity.
To effectively organize inventory using industrial shelving solutions, there are several key considerations to keep in mind:
- Categorization: Grouping similar items together based on factors like size, weight, or product type allows for easier identification and retrieval. This categorization can be achieved through color-coded labels or designated sections within the shelving system.
- Accessibility: Placing frequently used items at eye level or within easy reach reduces unnecessary bending or reaching overhead during retrieval. This not only saves time but also minimizes the risk of accidents caused by strained movements.
- Flexibility: Opting for adjustable shelves or modular shelving units enables businesses to adapt their storage setup as inventory requirements change over time. This flexibility ensures that available space is utilized optimally without compromising safety or accessibility.
- Safety Measures: Implementing safety features such as guardrails, non-slip flooring surfaces near shelving units, and load capacity indicators helps prevent accidents and protects both employees and stored inventory from damage.
Benefit | Description |
---|---|
Increased Efficiency | Properly organized inventory enables faster picking times and reduces downtime caused by search delays. |
Enhanced Productivity | Streamlined retrieval processes allow employees to focus on value-added tasks, boosting overall output. |
Reduced Inventory Loss | By minimizing mishandling and damage risks through organized storage, businesses can reduce financial losses associated with inventory replacement or repair. |
Improved Workplace Safety | Well-structured shelving systems promote a safer work environment by preventing accidents and injuries related to falling objects or inefficient movement around the warehouse. |
Incorporating these considerations into their inventory organization strategy allowed our hypothetical automotive parts manufacturer to realize significant improvements in efficiency, productivity, safety, and cost-effectiveness.
With an understanding of the benefits that industrial shelving solutions offer for efficient inventory organization, it is now essential to explore how implementing a maintenance plan for these shelves can further enhance their longevity and functionality
Implementing a Maintenance Plan for Industrial Shelving
Transition from the previous section:
Having explored how industrial shelving can effectively organize inventory, it is crucial to establish a comprehensive maintenance plan for these storage solutions. By implementing regular upkeep and monitoring practices, businesses can ensure their shelves remain in optimal condition, maximizing efficiency and longevity.
Section Title: Implementing a Maintenance Plan for Industrial Shelving
To illustrate the importance of a proper maintenance plan, let’s consider a hypothetical scenario where a manufacturing facility fails to prioritize shelf upkeep. Over time, dust accumulates on the shelves’ surfaces, obstructing visibility and increasing the risk of items falling or becoming misplaced. This negligence not only hampers productivity but also poses safety hazards for employees who rely on efficient access to stored materials.
To prevent such issues and maintain an organized workspace, businesses should incorporate a well-rounded maintenance plan that includes the following key elements:
- Regular Cleaning: Dust and debris accumulation compromises both aesthetics and functionality. Establish routine cleaning schedules to remove dirt from shelves using appropriate cleaning agents or methods suitable for the material used in construction.
- Inspection Protocols: Conduct periodic inspections to identify any signs of damage or wear on shelving components such as brackets, beams, or wire mesh decks. Promptly address any structural weaknesses by repairing or replacing affected parts.
- Load Capacity Assessments: Regularly evaluate load capacities based on manufacturers’ guidelines and industry standards. Ensure that weight limits are not exceeded to prevent overloading which could lead to shelving collapse or uneven distribution of goods.
- Employee Training: Educate staff members about proper usage and handling techniques specific to different types of industrial shelving systems. Promote safe practices like evenly distributing loads across shelves and avoiding placing heavy objects on upper levels.
Incorporating these elements into your maintenance plan will help safeguard your investment in industrial shelving while promoting workplace safety and efficiency.
Maintenance Checklist | Frequency |
---|---|
Dusting shelves | Weekly |
Inspecting components | Monthly |
Assessing load limits | Quarterly |
Employee training | Annually |
By adhering to a comprehensive maintenance plan, businesses can extend the lifespan of their industrial shelving systems and mitigate potential risks. Regular cleaning, inspection, load assessments, and employee training form an integral part of proactive shelf management, ensuring a well-organized inventory storage solution that enhances productivity in the long run.
Remember, investing time and effort into maintaining your industrial shelving will ultimately save you from costly repairs or replacements down the line.