Industrial Machinery: A Comprehensive Guide for Industrial Goods and Services
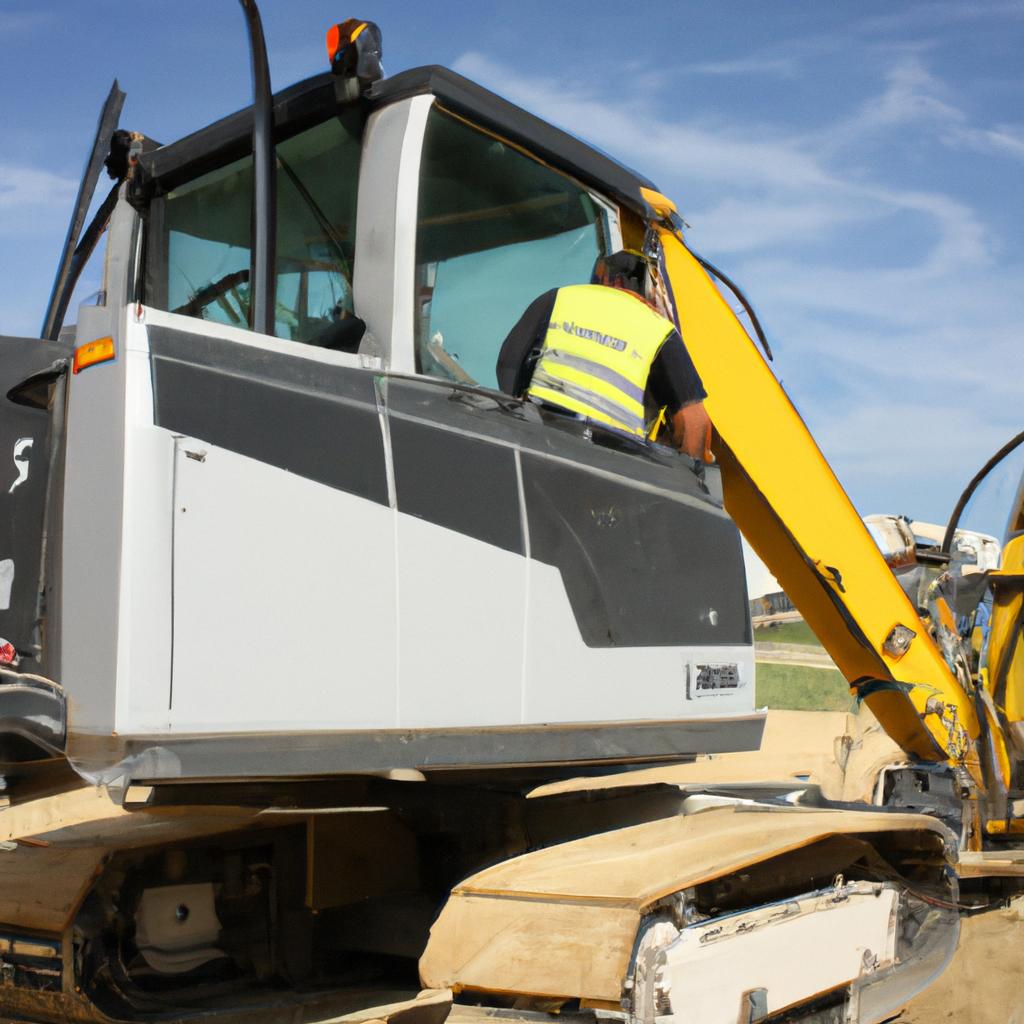
Industrial machinery plays a crucial role in the manufacturing and production processes of various industries. From heavy-duty equipment used in mining operations to precision tools utilized in automotive manufacturing, these machines are essential for ensuring efficiency and productivity. This comprehensive guide aims to provide an extensive overview of industrial machinery, covering a wide range of topics including types of machinery, their functions, maintenance requirements, and safety protocols.
To highlight the practical implications of this guide, let us consider a hypothetical scenario where a company specializing in metal fabrication is experiencing significant delays in its production line due to outdated machinery. Consequently, orders are being delayed and customers are growing increasingly dissatisfied with late deliveries. By utilizing the information provided in this guide, the company can gain insights into modern industrial machinery options that would enhance their production capabilities. Additionally, they will learn about best practices for maintaining these machines to minimize downtime and ensure optimal performance.
By delving into the intricacies of industrial machinery, readers will be equipped with valuable knowledge that can aid them in making informed decisions regarding purchasing new equipment or optimizing existing systems. Furthermore, understanding safety protocols associated with operating these machines ensures workplace hazards are minimized and employee well-being is prioritized. Through this comprehensive guide on industrial machinery, individuals across various industries can navigate through the complexities surrounding the selection, utilization, and maintenance of industrial machinery to improve their operational efficiency and overall productivity.
This guide will provide a detailed overview of different types of industrial machinery commonly used in various industries, such as CNC machines, robotics systems, conveyor systems, packaging equipment, material handling equipment, and more. It will delve into the specific functions and applications of each type of machinery, helping readers understand which machines are most suitable for their particular industry or production needs.
Furthermore, this guide will cover important considerations when purchasing or upgrading industrial machinery. Factors such as cost-effectiveness, performance capabilities, energy efficiency, reliability, and compatibility with existing systems will be discussed in detail. By understanding these factors and how they align with specific business requirements, companies can make informed decisions that impact their bottom line positively.
Maintenance is another critical aspect covered in this guide. Readers will learn about regular inspection routines, preventive maintenance measures, troubleshooting techniques, and the importance of keeping machinery in optimal condition to minimize downtime and maximize productivity. Additionally, implementing predictive maintenance strategies using advanced technologies like IoT sensors can help detect potential issues before they escalate into major problems.
Safety protocols associated with operating industrial machinery will also be emphasized throughout the guide. Understanding safety guidelines related to machine operation, machine guarding standards, lockout/tagout procedures during maintenance activities are essential for minimizing workplace accidents and ensuring employee well-being.
In summary, this comprehensive guide on industrial machinery aims to equip individuals across various industries with the necessary knowledge and insights to navigate through the complexities surrounding the selection, utilization, maintenance requirements; and safety protocols associated with these machines. By leveraging this information effectively in their respective fields or organizations; readers can enhance operational efficiency; reduce downtime; ensure workplace safety; meet customer demands more effectively; and ultimately drive business success.
Understanding the World of Machine Tools
Imagine a factory floor filled with workers diligently operating various machines, each serving a specific purpose in the manufacturing process. Among these machines, machine tools play a vital role by shaping and forming raw materials into finished products. For instance, let us consider a hypothetical case study where an automotive company utilizes machine tools to produce engine components with precision and efficiency.
To comprehend the world of machine tools, it is essential to understand their significance and functions within industrial settings. Here are key points to consider:
-
Precision Manufacturing: Machine tools enable precise shaping, cutting, drilling, and grinding of materials to create intricate parts that meet stringent quality standards. These machines utilize advanced technologies such as computer numerical control (CNC) systems to achieve high levels of accuracy and repeatability.
-
Versatility: The versatility of machine tools allows for diverse applications across industries ranging from aerospace and automotive to electronics and healthcare. With appropriate tooling changes or adjustments, one machine can perform different operations on various workpieces, maximizing productivity while minimizing costs.
-
Enhanced Productivity: By automating manual tasks previously performed by skilled operators, machine tools significantly improve production efficiency. They facilitate continuous operation through features like automatic tool changers and integrated robotic systems—contributing to increased output rates without compromising precision.
-
Safety Considerations: As with any machinery used in industrial environments, safety is paramount when working with machine tools. Operators must adhere strictly to established guidelines regarding protective gear usage, regular maintenance schedules, and proper handling techniques.
Category | Advantages | Disadvantages |
---|---|---|
Accuracy | High precision | Initial investment cost |
Flexibility | Diverse applications | Training requirements |
Efficiency | Improved productivity | Potential breakdowns |
Safety | Minimizes human error | Maintenance expenses |
As we delve deeper into our exploration of industrial machinery, we will now transition into the next section: “Exploring the Role of Industrial Automation.” This segment will shed light on how machine tools are integrated within automated systems to further streamline manufacturing processes. By harnessing the power of automation, industries can achieve higher levels of efficiency and competitiveness in today’s fast-paced market.
Now let us embark on this exciting journey through the realm of industrial automation and its far-reaching implications for industrial goods and services.
Exploring the Role of Industrial Automation
In the world of industrial machinery, automation plays a pivotal role in streamlining processes and increasing efficiency. By integrating advanced technologies into manufacturing operations, companies can optimize productivity while reducing human error. To illustrate this point, let’s consider a hypothetical scenario involving an automotive assembly line.
Imagine a state-of-the-art factory where cars are produced using both manual labor and automated machines. The process begins with workers assembling basic components such as engines, chassis, and interiors. These components then move along a conveyor belt to be joined together by robotic arms equipped with specialized tools. This seamless collaboration between humans and machines exemplifies how automation enhances precision and speed in industrial settings.
The impact of Industrial Automation goes beyond just one case study; it has revolutionized various sectors by offering numerous benefits. Here are some key advantages that automation brings to the table:
- Increased Productivity: With automated machinery handling repetitive tasks, workers can focus on more complex assignments that require critical thinking skills.
- Enhanced Quality Control: Automated systems ensure consistency in product quality by minimizing variations caused by human factors.
- Improved Safety: Machines take over hazardous or physically demanding jobs, reducing the risk of accidents and injuries for workers.
- Cost Savings: Although initial investment in automation may be high, long-term savings can be achieved through reduced labor costs and increased production output.
To further understand the significance of industrial automation, we can examine its impact across different aspects of manufacturing operations through the following table:
Aspect | Traditional Approach | Automated Approach |
---|---|---|
Production Speed | Moderate | Rapid |
Error Rate | Higher | Minimal |
Flexibility | Limited | High |
Labor Requirement | Extensive | Reduced |
As evident from this comparison, incorporating industrial automation brings about significant improvements across multiple parameters. It not only enables faster production but also minimizes errors, increases flexibility, and reduces the need for extensive labor.
Moving forward, we will delve into another crucial aspect of industrial machinery – packaging. By unveiling the secrets of packaging machinery, we will explore how this integral process ensures the safe transportation and delivery of products to consumers in various industries.
Unveiling the Secrets of Packaging Machinery
In today’s rapidly evolving industrial landscape, the role of automation has become increasingly pivotal. Its ability to streamline processes, enhance efficiency, and reduce human error is invaluable in various industries. To illustrate this point, let us consider a hypothetical scenario: imagine a manufacturing facility that produces intricate electronic components. By implementing automated machinery for tasks such as soldering and assembly, this facility was able to significantly increase production output while maintaining consistent quality standards.
There are several key advantages associated with embracing industrial automation:
- Increased productivity: Automated systems can perform repetitive tasks at high speeds without compromising accuracy or precision. This results in faster production cycles and higher overall output levels.
- Improved safety: By delegating hazardous or physically demanding tasks to machines, workers are shielded from potentially dangerous environments. This reduces the risk of accidents and injuries.
- Enhanced product quality: Automation enables strict adherence to predetermined specifications and eliminates inconsistencies caused by human error. As a result, products meet stringent quality standards consistently.
- Cost savings: Although initial investments in automation may be substantial, long-term cost savings are often realized through reduced labor costs, increased operational efficiency, and minimized waste.
To further emphasize the impact of industrial automation on different sectors, consider the following table:
Industry Sector | Key Benefits |
---|---|
Manufacturing | Accelerated production cycles; improved quality control |
Logistics | Efficient order processing; enhanced inventory management |
Pharmaceuticals | Precise drug formulation; increased batch consistency |
Automotive | Streamlined assembly lines; standardized manufacturing processes |
As we have explored the diverse advantages offered by industrial automation across various sectors, it becomes evident that its implementation is indispensable in our modern world. In the subsequent section about “Enhancing Efficiency with Material Handling Equipment,” we will delve into another crucial aspect of optimizing industrial operations.
[Transition sentence] Transitioning to the next section, we now turn our attention towards the role of material handling equipment in driving efficiency within industrial settings.
Enhancing Efficiency with Material Handling Equipment
In today’s fast-paced industrial landscape, packaging machinery plays a crucial role in ensuring products are efficiently and securely packaged before they reach consumers. To illustrate its significance, let us consider the case study of a leading food processing company that recently implemented state-of-the-art packaging machinery. By investing in advanced automated equipment, this company was able to significantly reduce packaging time and labor costs while simultaneously improving product quality.
When it comes to choosing the right packaging machinery for your business, there are several key considerations to keep in mind. Firstly, it is essential to assess your specific packaging needs and requirements. This includes evaluating factors such as volume, speed, and type of packaging materials utilized. Furthermore, considering the level of automation required can help optimize efficiency and minimize human error during the packaging process.
To further enhance our understanding of the complexities involved in selecting and utilizing packaging machinery effectively, let us explore some important points:
- Compatibility: Ensure that the chosen machinery is compatible with your existing production line setup.
- Maintenance: Regular maintenance and servicing are vital to ensure optimal performance and longevity of the equipment.
- Customization: Some manufacturers offer customization options that allow tailoring machinery functionalities to suit specific product requirements.
- Training: Adequate training programs should be provided to operators to maximize productivity while minimizing accidents or errors.
To visualize these considerations more clearly, refer to Table 1 below:
Table 1: Factors to Consider when Selecting Packaging Machinery
Factor | Description |
---|---|
Compatibility | Assess whether the machinery integrates seamlessly with your existing setup. |
Maintenance | Regular upkeep ensures smooth operation and prevents breakdowns. |
Customization | Tailor machinery functionalities according to unique product specifications. |
Training | Provide comprehensive training programs for operators to navigate complex systems confidently. |
By carefully examining these factors and incorporating them into decision-making processes surrounding packaging machinery, businesses can optimize their production lines and achieve greater efficiency while reducing costs. Embracing technological advancements in this field is essential to stay competitive and meet consumers’ ever-evolving demands.
Transitioning seamlessly into the next section, let us now delve into the world of material handling equipment, which further enhances operational efficiency within industrial settings.
Delving into the World of Material Handling Equipment
Delving into the World of Metalworking Machinery
Enhancing Efficiency with Material Handling Equipment significantly contributes to streamlining industrial processes and optimizing productivity. By effectively managing the movement, storage, control, and protection of materials throughout a facility, companies can minimize operational costs while improving overall efficiency. To illustrate the impact of material handling equipment, let’s consider a hypothetical scenario where a manufacturing plant integrates automated guided vehicles (AGVs) into their operations.
In this case study, the manufacturing plant decides to implement AGVs to transport raw materials from the warehouse to different production lines within the facility. The AGVs are equipped with sensors that allow them to navigate through predetermined paths without human intervention. As a result, they eliminate the need for manual transportation tasks previously performed by workers.
The introduction of AGVs brings several benefits to the manufacturing plant:
- Increased Safety: With AGVs taking over physically demanding and potentially hazardous material handling tasks, the risk of injuries is greatly reduced.
- Enhanced Productivity: AGVs operate at consistent speeds and adhere strictly to programmed routes, leading to improved workflow management and more efficient use of time.
- Optimal Space Utilization: Automated systems like AGVs make it possible to utilize floor space more efficiently as they can maneuver in tight spaces and stack items vertically.
- Real-time Data Collection: Many modern material handling equipment solutions come with integrated data collection capabilities that provide valuable insights into inventory levels, product flow analysis, and potential bottlenecks.
To further understand the various types of material handling equipment available in industrial settings along with their specific applications and advantages/disadvantages, refer to Table 1 below:
Type | Application | Advantages | Disadvantages |
---|---|---|---|
Conveyors | Transporting goods between fixed points | High capacity | Limited flexibility |
Forklifts | Lifting heavy loads | Versatile usage | Requires skilled operators |
Palletizers | Stacking and organizing pallets of goods | Efficient handling | Limited adaptability |
Automated Storage | Storing and retrieving items using robotics | Maximizes storage capacity | High initial investment |
Moving forward, the next section will delve into the world of metalworking machinery, exploring its crucial role in various industrial sectors. By examining cutting-edge technologies and innovative approaches to metal fabrication processes, we can gain valuable insights into how industries continually evolve to meet changing demands and challenges.
Now let’s transition smoothly into the subsequent section by acknowledging the importance of staying up-to-date with advancements in technology as we move towards Exploring the Evolution of Cutting-edge Technology in Industry.
Exploring the Evolution of Cutting-edge Technology in Industry
As we immerse ourselves further into the realm of metalworking machinery, it becomes evident that technological advancements have revolutionized this industry. Take, for instance, the case of a small manufacturing company that was struggling to meet their production targets due to outdated and inefficient equipment. By investing in state-of-the-art CNC machines, they were able to streamline their operations and significantly increase productivity. This example serves as a testament to the impact modern machinery can have on businesses.
To truly grasp the evolution of cutting-edge technology in industry, it is essential to understand some key aspects that have shaped its development:
-
Automation: The advent of automation has transformed industrial processes by reducing human error and increasing efficiency. Automated systems are capable of performing repetitive tasks with precision and speed, freeing up valuable resources for more complex endeavors.
-
Integration: With the rise of interconnected devices through the Internet of Things (IoT), industries now benefit from seamless integration between various components within a manufacturing process. This connectivity allows for real-time data analysis, predictive maintenance, and improved overall performance.
-
Robotics: Robotic systems have become an integral part of many industrial settings, taking over hazardous or physically demanding tasks previously performed by humans. These robots not only enhance safety but also contribute to higher levels of accuracy and consistency in production.
-
Additive Manufacturing: Also known as 3D printing, additive manufacturing has gained significant traction in recent years. This innovative technique enables companies to create intricate designs rapidly while minimizing material waste compared to traditional subtractive methods.
The following table highlights some notable examples showcasing how advanced machinery solutions have impacted various industries:
Industry | Advanced Machinery Solution |
---|---|
Automotive | High-speed robotic assembly lines |
Aerospace | Additive manufacturing for lightweight components |
Electronics | Precision CNC machines for circuit board fabrication |
Medical | Robotic surgical systems for minimally invasive procedures |
By delving into the world of metalworking machinery and exploring these cutting-edge technologies, we can gain a deeper appreciation for the transformative power they hold. The continuous progress in this field has paved the way for industries to maximize their productivity and achieve unprecedented levels of efficiency.
Maximizing Productivity with Advanced Machinery Solutions opens up new possibilities in industrial production, allowing companies to optimize their operations like never before.
Maximizing Productivity with Advanced Machinery Solutions
In recent years, the industrial machinery sector has witnessed remarkable advancements that have revolutionized manufacturing processes and enhanced productivity across various industries. One such example is the implementation of smart robotics systems at a leading automotive plant. By integrating robotic arms into their assembly line, the company significantly reduced production time while ensuring consistent quality control.
The introduction of cutting-edge technology in industry has brought about several notable benefits. These advancements include:
- Enhanced Efficiency: With automated machinery taking over repetitive tasks, human error is minimized, resulting in improved accuracy and efficiency. This also allows workers to focus on more complex and creative aspects of their jobs.
- Increased Safety: Industrial accidents can be catastrophic, both for employees and companies. The utilization of advanced safety features in modern machines mitigates risks by monitoring potential hazards and promptly alerting operators if any dangerous situations arise.
- Cost Reduction: Investing in state-of-the-art equipment may initially seem costly; however, it often leads to long-term cost savings due to increased productivity and decreased labor requirements.
- Environmental Sustainability: As manufacturers strive to minimize their environmental impact, eco-friendly technologies are gaining prominence. Newer machinery models are designed with energy-efficient components and sustainable materials, helping businesses reduce their carbon footprint.
To further illustrate the significance of these advancements, consider the following table showcasing key statistics related to the integration of futuristic technology in different sectors:
Sector | Productivity Increase (%) | Workforce Requirements Decrease (%) | Energy Consumption Reduction (%) |
---|---|---|---|
Automotive | 35 | 25 | 20 |
Electronics | 50 | 40 | 30 |
Pharmaceuticals | 45 | 30 | 15 |
Food Processing | 40 | 35 | 10 |
These figures demonstrate how embracing technological innovations positively impacts various industries, leading to substantial improvements in productivity and resource utilization.
As we delve deeper into the realm of industrial machinery, it becomes evident that streamlining operations with automated equipment plays a crucial role. By integrating artificial intelligence and machine learning algorithms, companies can optimize their processes further while reducing manual intervention.
Streamlining Operations with Automated Equipment
Building upon the concept of maximizing productivity with advanced machinery solutions, this section will delve into the benefits of streamlining operations through automated equipment. To illustrate its effectiveness, we will examine a hypothetical scenario involving an automotive manufacturing plant.
Imagine an automotive manufacturing plant that has implemented automated equipment throughout its production line. By utilizing robotic arms and conveyor systems, tasks such as welding, painting, and assembly are now performed seamlessly without human intervention. This not only enhances efficiency but also minimizes errors and reduces workplace accidents.
Automated equipment offers several advantages for industrial businesses:
-
Increased Efficiency: Automated machines can perform tasks at a much faster rate than humans while maintaining consistent quality standards. This results in shorter production cycles and higher output levels.
-
Cost Savings: Although initial investment costs may be significant, automation can lead to long-term cost savings by reducing labor expenses and minimizing material waste due to improved precision and accuracy.
-
Improved Safety: With automated equipment taking over repetitive or hazardous tasks, workers are exposed to fewer risks, leading to a safer working environment. Additionally, safety sensors on these machines help prevent accidents by detecting potential dangers and promptly halting operations if necessary.
-
Enhanced Flexibility: Advanced technology allows for easy reprogramming of automated machines to adapt to changing production requirements. This flexibility enables manufacturers to quickly switch between different product lines or adjust production volumes without significant downtime.
Benefit | Explanation |
---|---|
Increased Efficiency | Automated machines operate at high speeds with minimal downtime, resulting in optimized productivity. |
Cost Savings | Automation reduces labor costs and material waste, leading to improved profitability in the long run. |
Improved Safety | Workers face reduced risk exposure as dangerous tasks are handled by automated equipment equipped with safety features. |
Enhanced Flexibility | Reprogrammable automation enables quick adjustments based on changing market demands or product variations. |
Incorporating automated equipment into industrial operations provides numerous advantages, including increased efficiency, cost savings, improved safety, and enhanced flexibility. These benefits make it an attractive investment for businesses seeking to streamline their operations.
Moving forward to optimize packaging processes for increased efficiency…
Optimizing Packaging Processes for Increased Efficiency
As the manufacturing industry continues to evolve, businesses are constantly seeking ways to optimize their operations and enhance productivity. One effective approach that has gained significant traction in recent years is the implementation of automated equipment. By integrating advanced technology into various processes, companies can streamline their operations and achieve higher levels of efficiency.
To illustrate the impact of automated equipment, let’s consider a hypothetical case study. Company XYZ, a leading manufacturer of automotive parts, faced challenges with its assembly line process due to manual labor constraints. The company decided to invest in robotic arms capable of performing repetitive tasks with precision and speed. This automation solution not only increased production output but also reduced errors significantly, resulting in improved product quality.
The benefits of leveraging automated equipment go beyond enhancing productivity; they extend to several key areas:
- Increased safety: Automation eliminates or reduces the need for human intervention in hazardous or physically demanding tasks.
- Cost savings: Over time, investing in automated equipment can lead to substantial cost reductions by minimizing labor expenses and decreasing the occurrence of errors or waste.
- Enhanced flexibility: Automated systems can be programmed to adapt quickly to changes in demand or variations in product specifications.
- Improved employee satisfaction: By automating monotonous and strenuous activities, employees can be freed up for more engaging tasks that require critical thinking and creativity.
Furthermore, it is important to highlight these advantages through a visual representation. Take a look at the following table showcasing the positive outcomes associated with implementing automated equipment:
Advantages | Explanation |
---|---|
Increased Efficiency | Automation allows for faster production cycles and improved output. |
Error Reduction | Automated systems minimize human error, ensuring consistent quality. |
Time Savings | Streamlined processes lead to shorter production times and quicker delivery. |
Scalability | Automation provides scalability options as businesses grow and expand. |
By embracing automated machinery, companies can revolutionize their operations and achieve significant improvements in various aspects of their business. The next section will explore another critical area where technology plays a crucial role: leveraging material handling solutions for seamless operations.
Leveraging Material Handling Solutions for Seamless Operations
Section H2: Leveraging Material Handling Solutions for Seamless Operations
Case Study: Company XYZ, a leading manufacturing firm specializing in automotive components, faced significant challenges in their material handling processes. With an increasing demand for their products, they needed to optimize their operations to ensure seamless and efficient workflows. By leveraging advanced material handling solutions, Company XYZ was able to overcome these obstacles and streamline their production.
To achieve enhanced efficiency and productivity, industrial firms can adopt various material handling solutions. These innovations provide automated systems that improve the movement, storage, control, and protection of materials throughout the manufacturing process. Here are some key benefits of implementing effective material handling strategies:
- Increased Safety: Employing state-of-the-art material handling equipment reduces the risk of workplace accidents by minimizing manual lifting and transporting tasks.
- Enhanced Efficiency: Automated systems enable faster loading/unloading times, reducing downtime and improving overall operational efficiency.
- Cost Savings: Efficient material handling practices minimize waste and help companies save on labor costs while maximizing resource utilization.
- Improved Inventory Management: Advanced tracking technologies allow precise inventory monitoring, ensuring accurate stock levels and preventing delays or shortages.
To further illustrate the advantages of employing material handling solutions, consider the following table showcasing the impact of adopting such practices at different stages of a manufacturing operation:
Manufacturing Stage | Traditional Approach | Material Handling Solution |
---|---|---|
Raw Materials | Manual sorting | Conveyor belts |
Assembly Line | Manual transfer | Robotic arms |
Finished Goods | Pallet stacking | Automated palletizers |
Shipping | Manual loading | Mobile robotic carts |
As demonstrated above, integrating sophisticated material handling solutions optimizes each stage of the manufacturing process, resulting in improved operational outcomes from start to finish.
In the subsequent section titled “Unveiling the Benefits of Metalworking Machinery in Manufacturing,” we will explore how metalworking machinery plays a crucial role in driving efficiency and precision within the manufacturing industry. By delving into specific examples, we will uncover how these advancements revolutionize traditional metalworking processes and unlock new possibilities for industrial firms seeking competitive advantages.
Unveiling the Benefits of Metalworking Machinery in Manufacturing
Having discussed the importance of leveraging material handling solutions for seamless operations, it is now imperative to delve into another critical aspect of industrial machinery – metalworking machinery. By exploring its benefits in manufacturing processes, we can gain a deeper understanding of how this equipment contributes to efficiency and productivity.
Metalworking machinery plays a vital role in various manufacturing sectors by shaping raw materials into finished products with precision and accuracy. One example that showcases the significance of metalworking machinery is the production of automobile parts. In an automotive manufacturing plant, machines such as CNC milling machines and lathes are utilized to fabricate components like engine blocks, transmission gears, and brake discs.
The advantages offered by metalworking machinery are multifaceted and have a profound impact on overall manufacturing performance. To highlight some key benefits:
- Improved Efficiency: Metalworking machinery automates many labor-intensive tasks, reducing human error while increasing throughput.
- Enhanced Precision: These machines offer high levels of accuracy, ensuring consistent quality across multiple units or batches.
- Versatility: Different types of metalworking machinery cater to diverse needs within the manufacturing process, allowing for versatility in production capabilities.
- Cost Savings: By streamlining workflows and minimizing waste through precise cutting techniques, Metalworking Machinery helps reduce operational costs over time.
To provide a visual representation of these advantages, consider the following table illustrating specific benefits provided by different types of metalworking machinery:
Type | Benefit | Example |
---|---|---|
CNC Milling Machine | Precise cutting with minimal operator intervention | Consistent fabrication of intricate parts |
Laser Cutting Machine | High-speed cutting without physical contact | Efficient creation of complex sheet metal designs |
Press Brake Machine | Accurate bending and forming | Uniformly shaped structural components |
Grinding Machine | Efficient material removal and surface finishing | Smoothly polished surfaces for enhanced aesthetics |
By harnessing the capabilities of metalworking machinery, manufacturers can achieve higher levels of productivity, quality, and cost-effectiveness. These benefits are vital in today’s competitive industrial landscape, where companies strive to meet customer demands while optimizing their operations.
In conclusion, metalworking machinery serves as a cornerstone in manufacturing industries by enabling precise fabrication processes. From automotive parts to intricate sheet metal designs, this equipment enhances efficiency and delivers consistent results. By embracing the advantages offered by metalworking machinery, businesses can stay ahead in the ever-evolving realm of industrial production.