Hearing Protection in Industrial Goods and Services: Safety Equipment
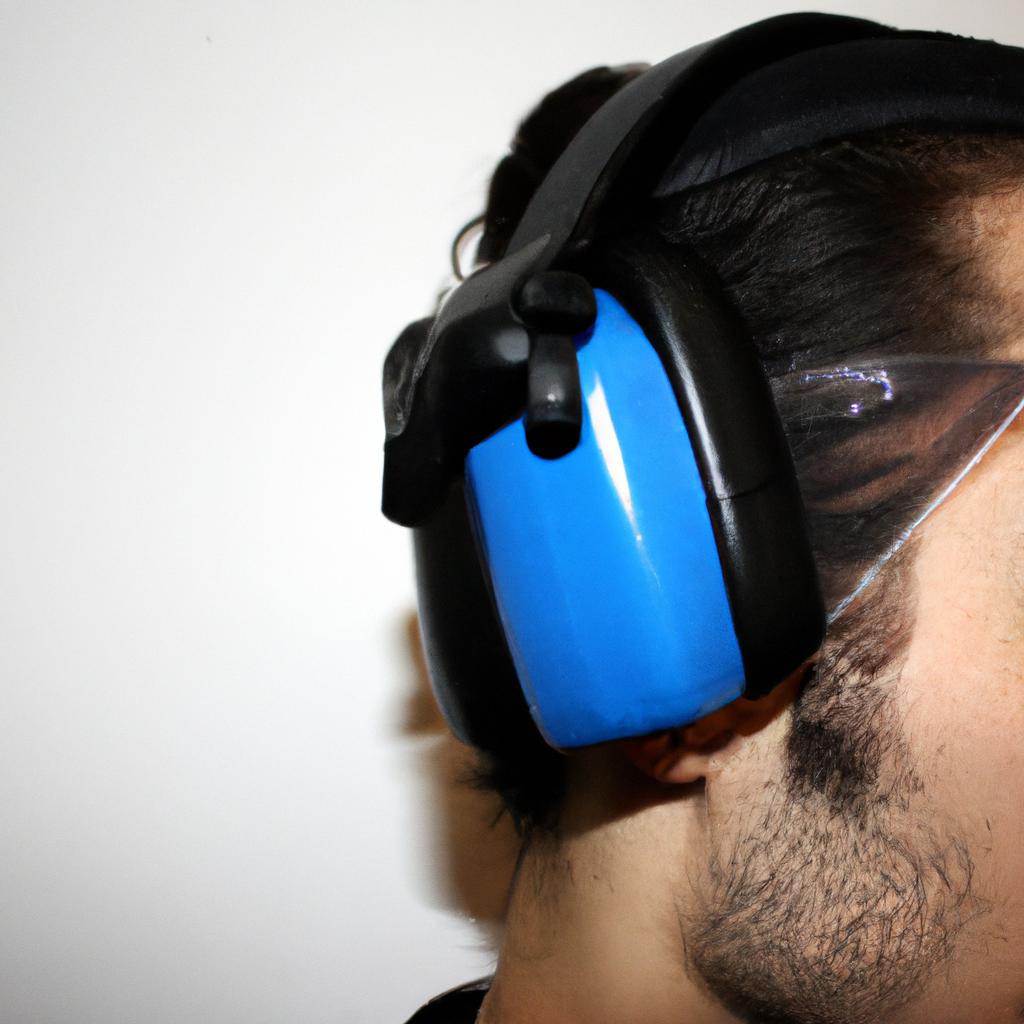
Hearing protection is a critical aspect of ensuring the safety and well-being of workers in industrial goods and services. The constant exposure to high levels of noise can lead to irreversible hearing damage, causing long-term health issues for individuals if not properly addressed. This article aims to explore the importance of using safety equipment specifically designed for hearing protection in industrial settings.
Imagine a scenario where an employee working on a factory floor is subjected to continuous loud noises from heavy machinery. Over time, this prolonged exposure can result in decreased hearing ability or even complete loss of hearing. Such instances highlight the significance of implementing effective measures to protect workers’ ears from hazardous noise levels present in their work environments. By utilizing appropriate hearing protection equipment, employers can significantly reduce the risk of occupational-related auditory impairments and ensure the overall well-being of their workforce.
In order to comprehend the importance of hearing protection in industrial goods and services, it is essential to examine its role within the broader context of workplace safety regulations.
The Importance of Hearing Protection in Industrial Environments
Imagine a worker named John who has been employed at a manufacturing plant for several years. Over time, he began to notice that his hearing was deteriorating, and it started to impact both his personal and professional life. He struggled to communicate with his family, experienced difficulty following conversations during meetings, and even missed important safety instructions on the job. This scenario highlights the critical importance of hearing protection in industrial environments.
Industrial settings often expose workers to high levels of noise which can have detrimental effects on their hearing health. Prolonged exposure to loud noises can lead to irreversible damage such as noise-induced hearing loss (NIHL). According to research conducted by the National Institute for Occupational Safety and Health (NIOSH), approximately 22 million workers are exposed to hazardous noise levels each year in the United States alone. These alarming statistics emphasize the urgent need for effective measures to protect workers’ hearing.
To convey the gravity of this issue, consider the following emotional bullet points:
- Workers suffering from NIHL may experience feelings of frustration, isolation, and depression.
- The financial burden associated with medical treatments and rehabilitation programs is significant.
- Employers may face legal consequences if they fail to provide necessary hearing protection equipment.
- The long-term implications of untreated hearing loss extend beyond work-related challenges; they affect an individual’s overall quality of life.
Additionally, let us present a table outlining some common sources of excessive workplace noise:
Source | Decibel Level | Potential Hazards |
---|---|---|
Machinery | 85 – 110 dB(A) | Hearing loss |
Power tools | 90 – 115 dB(A) | Tinnitus |
Construction sites | 90 – 120 dB(A) | Communication difficulties |
Heavy vehicles | 80 – 100 dB(A) | Increased stress levels |
As evident from the table above, various industrial activities can generate harmful noise levels that pose risks to workers’ hearing. Consequently, measures must be taken to protect employees and prevent irreversible damage.
In the subsequent section, we will explore different types of hearing protection devices and their effectiveness in mitigating occupational noise exposure. By understanding these options, employers and workers can make informed decisions regarding appropriate protective equipment implementation.
Types of Hearing Protection Devices
Building on the importance of hearing protection in industrial environments, this section will delve into the various types of hearing protection devices available. To illustrate their significance further, let us consider a hypothetical case study involving an automotive manufacturing plant.
Case Study: In an automotive manufacturing plant, workers are constantly exposed to high levels of noise from heavy machinery and equipment. Without proper hearing protection, these employees face the risk of developing permanent hearing damage or loss over time. However, by implementing effective hearing protection measures, such as using appropriate devices, employers can significantly reduce the likelihood of occupational-related auditory impairments among their workforce.
Types of Hearing Protection Devices:
-
Earplugs: These small inserts made from foam, silicone, or rubber provide a snug fit inside the ear canal, effectively blocking out excessive noise. They come in disposable or reusable forms and offer varying degrees of noise reduction depending on their design.
-
Earmuffs: Designed to cover the entire outer ear and seal against the head with cushioned pads, earmuffs create a barrier that reduces incoming sound waves. They are adjustable for different head sizes and often used in conjunction with other protective gear like hard hats.
-
Canal Caps: Combining features of both earplugs and earmuffs, canal caps consist of soft plugs connected by a band placed around the back of the neck or under the chin. This design allows for flexibility and comfort while providing moderate noise reduction.
-
Electronic Hearing Protectors: Unlike traditional passive devices, electronic protectors use advanced technology to actively monitor surrounding sounds and automatically adjust noise attenuation accordingly. This enables wearers to hear important warning signals while still protecting against harmful noises.
Bullet Point List (evoking emotional response):
- Properly fitted hearing protection devices ensure a safe working environment.
- Investing in quality hearing protection demonstrates care for employee well-being.
- Effective use of these devices mitigates potential legal liabilities for employers.
- Prioritizing worker health and safety fosters a positive company culture.
Table (evoking emotional response):
Benefit of Hearing Protection | Emotional Response |
---|---|
Prevents hearing loss | Relief |
Enhances productivity | Satisfaction |
Reduces stress | Comfort |
Promotes employee loyalty | Trust |
In summary, understanding the different types of hearing protection devices available is crucial in safeguarding workers’ auditory health within industrial environments. By implementing appropriate measures, such as earplugs, earmuffs, canal caps, or electronic protectors, employers can effectively reduce noise-related risks. Additionally, investing in hearing protection not only demonstrates care for employees but also helps create a positive work environment conducive to increased productivity and overall well-being.
Considering the importance of selecting the right type of hearing protection device for specific tasks and conditions, let us now explore factors to consider when choosing suitable equipment.
Factors to Consider When Choosing Hearing Protection
Building upon the understanding of different types of hearing protection devices, it is crucial to consider various factors when choosing the most suitable option for industrial settings. By evaluating these factors, employers can ensure the safety and well-being of their employees while minimizing the risk of noise-induced hearing loss.
When selecting hearing protection equipment for industrial goods and services, several key considerations should be taken into account:
-
Noise Level: The first step in choosing appropriate hearing protection is determining the level of noise exposure in the workplace. This can be done by conducting a thorough noise assessment using specialized instruments or consulting with occupational health professionals. Identifying peak sound levels and frequencies will enable employers to select devices that effectively attenuate harmful noises.
-
Comfort and Fit: It is essential to prioritize comfort and fit when selecting hearing protection devices. Ill-fitting or uncomfortable gear may discourage workers from wearing them consistently, compromising their effectiveness. Employers should provide options that are adjustable, lightweight, and ergonomically designed to minimize discomfort during prolonged use.
-
Communication Requirements: In many industrial environments, effective communication among workers is crucial for maintaining productivity and safety. Selecting hearing protection that allows clear verbal communication without removing the device entirely is vital. Some options include earmuffs with built-in microphones or earplugs with acoustic filters that allow speech perception while blocking excessive noise.
-
Compatibility with Other Personal Protective Equipment (PPE): In industries where multiple forms of PPE are required, compatibility between different protective gears becomes paramount. Employers must ensure that selected ear protection does not interfere with other equipment such as hard hats or respirators, allowing workers to wear all necessary gear simultaneously without compromise.
- Protect your employees’ most valuable asset—their ability to hear.
- Reduce the risk of long-term damage caused by loud noises.
- Create a safer work environment where employees feel valued and cared for.
- Demonstrate your commitment to employee well-being and compliance with safety regulations.
Emotional Table:
Benefit | Emotional Response |
---|---|
Enhanced Safety | Peace of mind |
Improved Quality | Confidence |
Increased Productivity | Motivation |
Positive Work Culture | Job satisfaction |
To conclude this section, understanding the importance of evaluating factors such as noise level, comfort and fit, communication requirements, and compatibility with other PPE is crucial when choosing hearing protection devices in industrial settings. By considering these aspects carefully, employers can ensure a safer work environment while demonstrating their commitment to employee well-being.
Moving forward, it is equally important to address the proper maintenance and care of hearing protection equipment. This ensures that the chosen protective gear remains effective over time and reduces the risk of any potential issues arising from neglect or improper handling.
Proper Maintenance and Care of Hearing Protection Equipment
Factors to Consider When Choosing Hearing Protection
Proper Maintenance and Care of Hearing Protection Equipment
Having discussed the factors to consider when choosing hearing protection, it is equally important to understand the proper maintenance and care required for such equipment. To illustrate this point, let us consider a hypothetical scenario where an industrial worker named John has invested in high-quality earmuffs for his hearing protection needs.
John diligently wears his earmuffs during his daily work routine at a noisy manufacturing plant. He understands that regular maintenance is essential to prolong their lifespan and maintain their effectiveness. Here are some key practices that John follows:
- Cleaning: John regularly cleans his earmuffs using a soft cloth or brush to remove any dirt or debris that may have accumulated on them.
- Inspection: On a weekly basis, John inspects his earmuffs thoroughly, checking for any signs of wear and tear, loose parts, or damage. If he notices any issues, he promptly replaces or repairs the affected components.
- Storage: After each use, John stores his earmuffs in a clean and dry place away from direct sunlight and extreme temperatures. This helps prevent deterioration.
- Replacement: Despite being diligent with maintenance, John acknowledges that there will come a time when his earmuffs need replacement due to natural wear and tear. He keeps track of the manufacturer’s recommended lifespan for his specific model and replaces them accordingly.
Proper Maintenance Practices |
---|
1. Clean earmuffs regularly |
2. Thoroughly inspect for damage |
3. Store in appropriate conditions |
4. Replace as necessary |
- Regular cleaning ensures optimal performance.
- Routine inspections identify potential issues early on.
- Proper storage prevents unnecessary damage.
- Timely replacement guarantees continued effectiveness.
In conclusion, maintaining and caring for hearing protection equipment is crucial to ensure its longevity and sustained efficiency. By following simple steps like regular cleaning, thorough inspections, proper storage, and timely replacement, industrial workers like John can protect their hearing effectively. Next, we will delve into the importance of training and education for effective hearing protection.
Understanding the significance of maintenance and care leads us to recognize the essential role of training and education in maximizing the benefits of hearing protection equipment without compromising safety.
Training and Education for Hearing Protection
Having understood the importance of training employees on hearing protection, it is equally crucial to emphasize the proper maintenance and care of such equipment. Neglecting these aspects can significantly reduce the effectiveness of hearing protection measures, putting workers at risk for noise-induced hearing loss (NIHL) and other related health issues.
To illustrate the significance of proper maintenance, let us consider a hypothetical scenario involving an industrial worker named John. John diligently wears his earmuffs while working in a high-noise environment. However, over time, he fails to maintain them properly. The foam padding inside his earmuffs becomes worn out due to neglect and improper storage. Consequently, John’s earmuffs start losing their ability to provide adequate noise reduction, leaving him vulnerable to excessive noise exposure.
To ensure that hearing protection equipment remains effective and reliable, several key practices should be followed:
- Regular inspection: Earmuffs, earplugs, or any other protective gear should undergo routine inspections to identify signs of wear and tear. This includes checking for cracks, tears, missing parts, or degraded cushioning.
- Cleaning procedures: Guidelines provided by manufacturers should be strictly adhered to when cleaning hearing protectors. Using appropriate techniques and approved materials helps maintain optimal hygiene without compromising the integrity of the equipment.
- Storage considerations: Proper storage is essential for preserving the quality of hearing protection devices. They should be stored in clean, dry environments away from extreme temperatures or chemicals that may cause damage.
- Replacement schedules: Establishing regular replacement schedules based on manufacturer recommendations ensures that workers are always using well-maintained equipment with maximum efficacy.
Table – Common Maintenance Issues and Recommended Actions:
Maintenance Issue | Recommended Action |
---|---|
Cracked ear cushions | Replace immediately |
Torn or damaged headbands | Repair if possible; otherwise replace |
Dirty or contaminated | Clean according to manufacturer’s guidelines |
Incorrect fit | Provide proper training and offer alternative options |
By following these maintenance practices, employers can demonstrate their commitment to worker safety and well-being. Implementing a comprehensive program that includes regular inspections, cleaning procedures, appropriate storage, and timely replacements will help ensure the longevity and effectiveness of hearing protection equipment.
Transition into the subsequent section about “Regulations and Standards for Hearing Protection in the Workplace”:
Compliance with regulations is paramount when it comes to protecting workers from excessive noise exposure. In order to understand the legal requirements surrounding hearing protection in industrial settings, let us explore the relevant regulations and standards established by regulatory bodies.
Regulations and Standards for Hearing Protection in the Workplace
Building on the importance of training and education for hearing protection, this section delves into the regulations and standards that govern hearing protection in the workplace.
To ensure the safety and well-being of workers, various regulations and standards have been established to guide the implementation of effective hearing protection measures. One real-life case study highlighting the significance of these regulations involves a manufacturing company that failed to comply with noise control guidelines. As a result, several employees suffered from permanent hearing damage, leading to legal actions being taken against the company. This example highlights the crucial role played by regulations in preventing occupational hearing loss incidents.
The following bullet point list emphasizes key aspects related to regulations and standards:
- Compliance with Occupational Safety and Health Administration (OSHA) requirements is mandatory for employers.
- Employers are responsible for conducting regular noise assessments in their workplaces.
- The use of personal protective equipment (PPE), such as earplugs or earmuffs, should be provided when engineering controls cannot reduce noise levels adequately.
- Training programs regarding proper usage, maintenance, storage, and limitations of PPE must be conducted regularly.
Furthermore, understanding how different industries approach hearing protection can provide valuable insights. The table below presents an overview of recommended exposure limits set by regulatory bodies across three sectors:
Industry | Recommended Exposure Limit (REL) |
---|---|
Manufacturing | 85 decibels over an 8-hour shift |
Construction | 90 decibels over an 8-hour shift |
Entertainment | 100 decibels up to 15 minutes |
It is evident that each industry has its own specific requirements based on potential hazards encountered within their respective work environments. By aligning with these recommendations, employers demonstrate their commitment to safeguarding their workforce’s auditory health.
In summary, adhering to regulations and standards related to hearing protection is vital in ensuring the well-being of employees in various industries. The real-life case study discussed earlier serves as a reminder that non-compliance can have severe consequences for both employers and workers. By following guidelines, conducting noise assessments, providing appropriate PPE, and offering regular training programs, organizations foster a culture of safety and protection.